
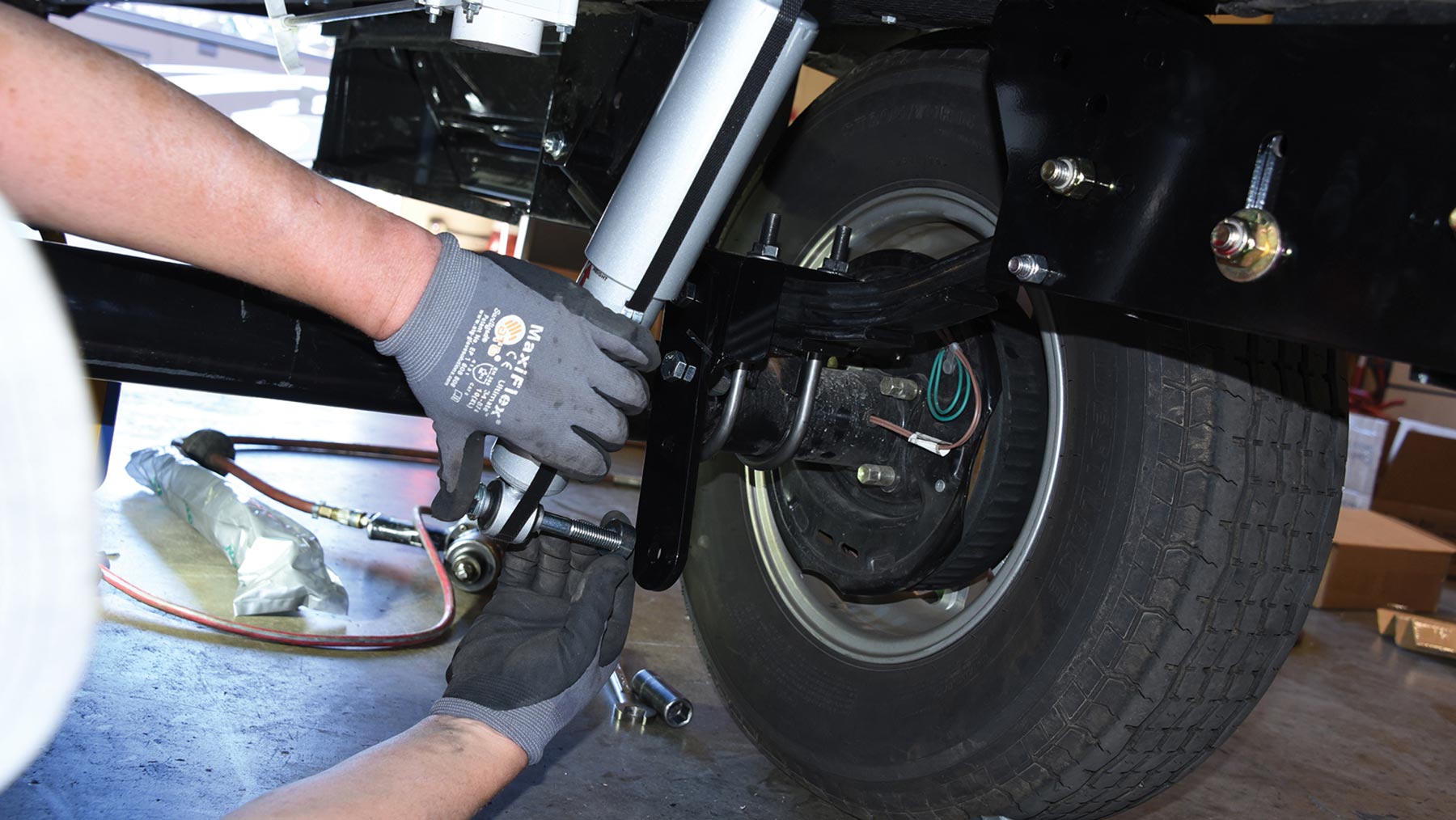
raveling by RV represents, in many ways, the pinnacle of freedom. Whether you’re heading out for just a long weekend or a months-long adventure, it’s tough to minimize having the ability to just pick up your “home” and head off to virtually anywhere the road can take you.
Well, until something breaks. Rather than become frustrated at the mostly unavoidable result of a machine succumbing to inevitable wear-and-tear, however, RVers might well look upon their RV as something that can not only be personalized but improved upon. Unless you’ve got deep pockets, most RVs are a compromise between what it could be and what it is — and we’re not just speaking about the difference between, say, a nice linoleum floor covering and heated ceramic tiles. RV engineers, designers and product managers are constantly working to create the best vehicle they can — albeit within price point constraints. Ironically, though, the difference between a “good” and “better” product is sometimes just a few dollars, a situation that oftentimes leaves owners scratching their heads.
Consider, as a prime example, contemporary RV suspensions. That may in fact qualify as an oxymoron when you realize that the typical leaf-spring trailer suspension has been with us since the days of the horse and buggy, and even some motorhome suspensions are a bit long in the tooth. The fact that such designs are still used today demonstrates their capacity for endurance, if not comfort; fortunately, either can be dramatically improved without breaking the bank.
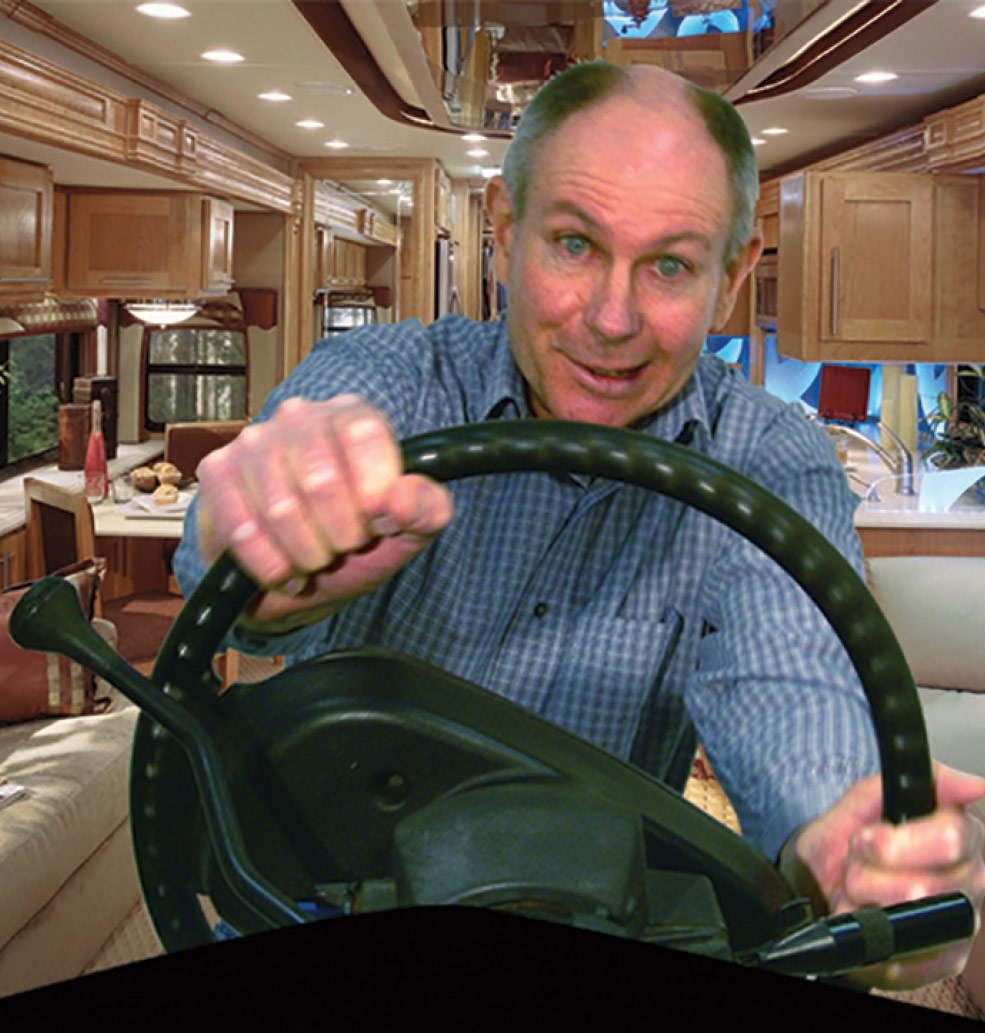
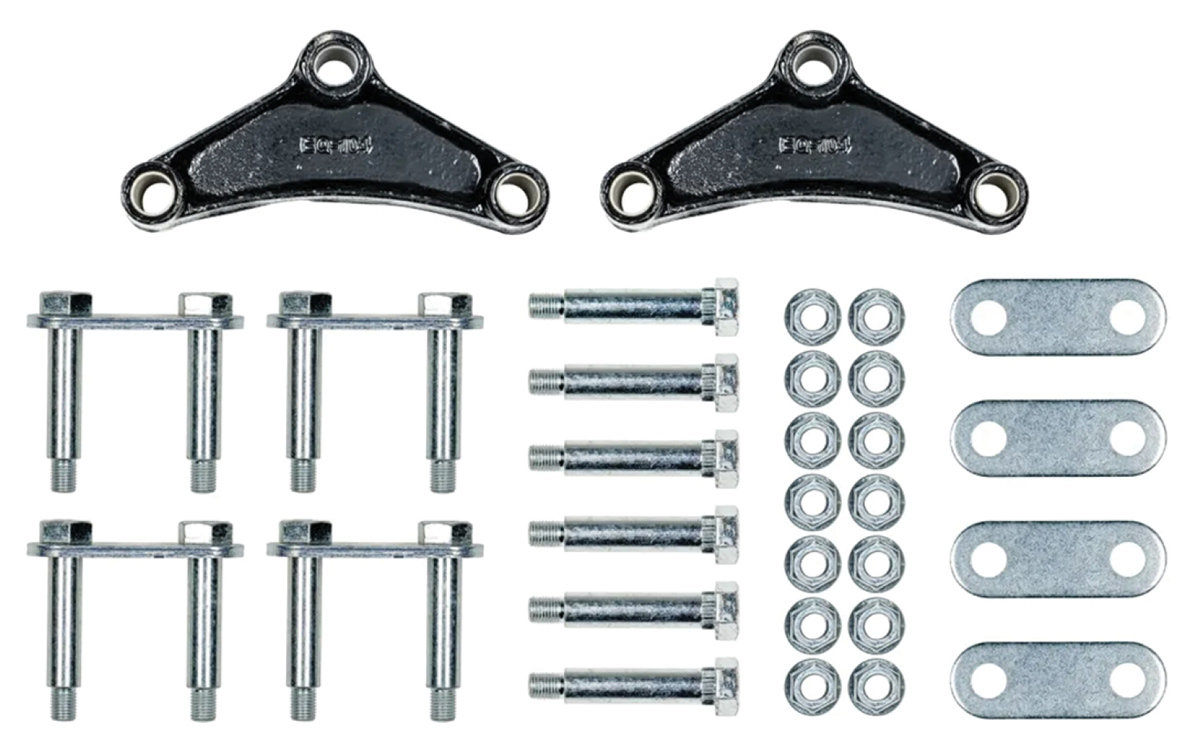
All things being equal, however, replacing worn components simply means that you will be restoring the stock ride. And as David Robinson, vice president of Roadmaster Inc. (roadmasterinc.com), pointed out, “there’s a reason why people don’t ride in trailers while traveling.” Again, however, improving upon your RV’s baseline suspension need not be prohibitively expensive (unless you truly want the best ride imaginable). Yes, systems exist that can seemingly turn rough roads into smooth glass, but as we learned when asking Robinson and MORryde’s (morryde.com) Sales and Marketing Manager Jack Enfield, certain components offer improvements seemingly well beyond their cost.
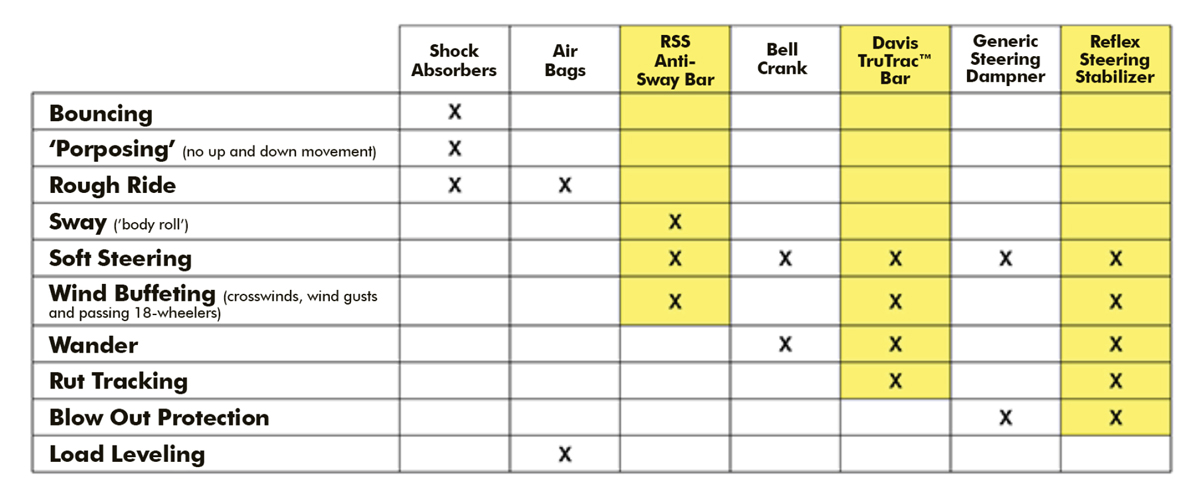
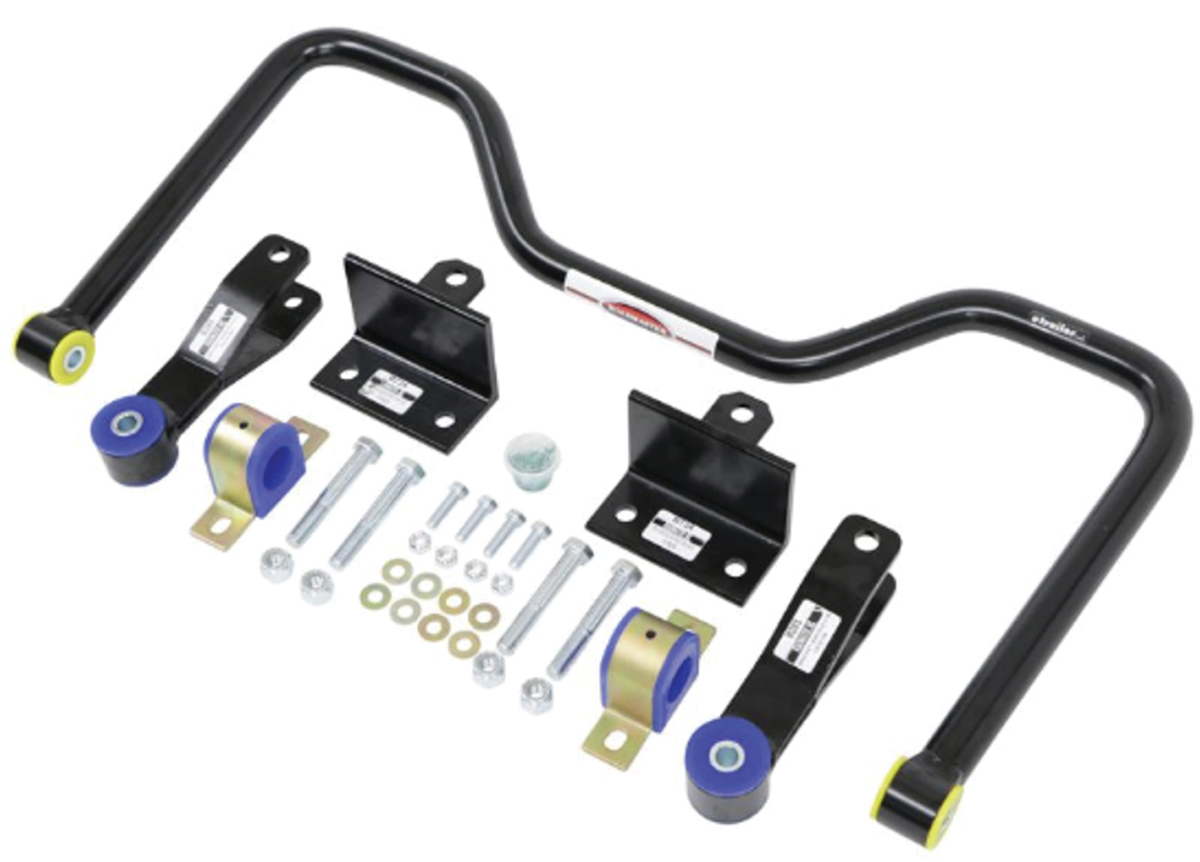
Asked to select one product that would reap the biggest benefits for motorhome owners, Robinson was to the point: a rear anti-sway bar.
“I could say ‘sway bars’ in general because Roadmaster makes them for both the front and rear, but if someone said, ‘Look, I don’t want to spend money to put product on both the front and the rear; which one delivers the most bang for the buck?,’ the rear sway bar is going give the most handling improvement of everything,” he said.
A problem prevalent in the industry, he noted, is what he calls the ‘big rig myth’ — because it’s a large motorhome, owners should expect it to handle poorly.
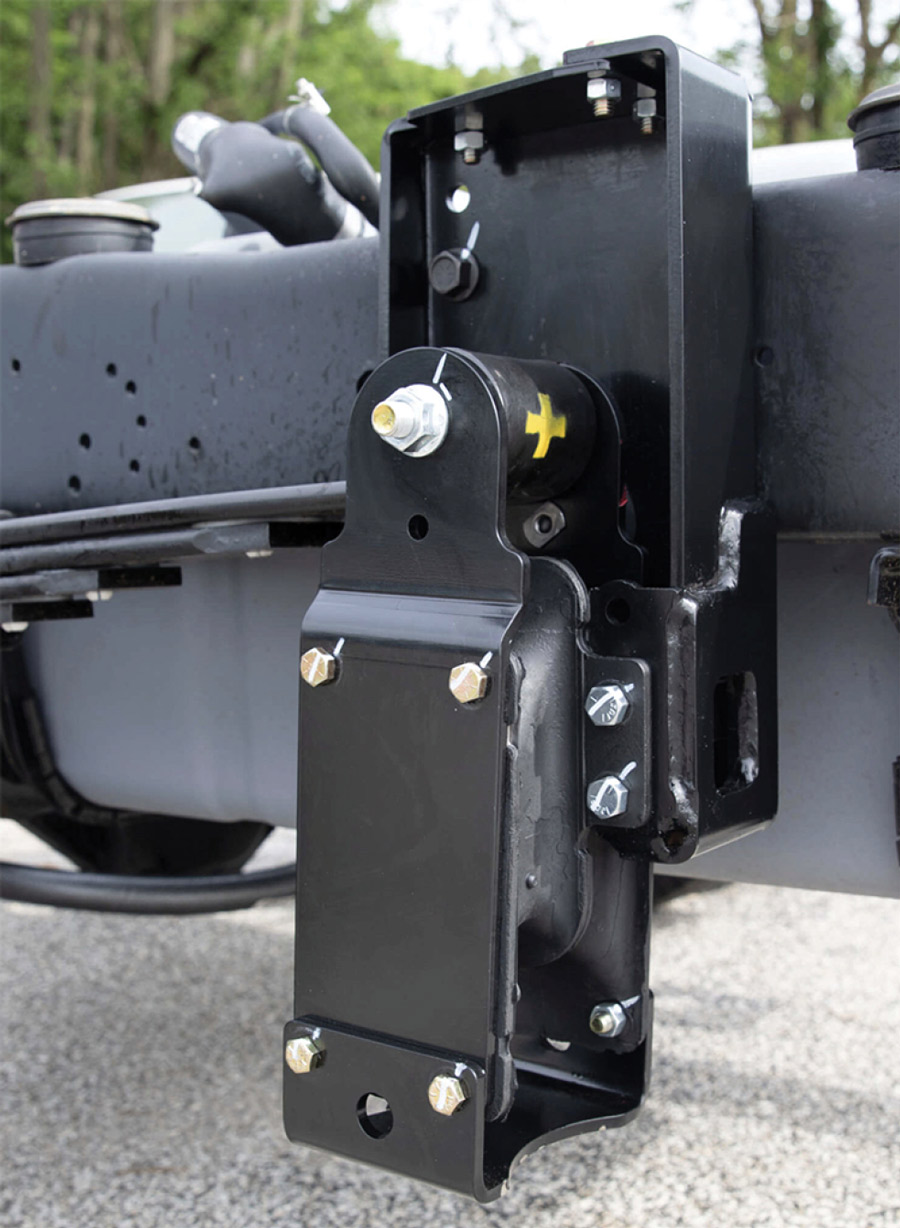
As Robinson explained, quite often in situations like that an owner will opt to add a steering stabilizer — but while it will help to correct those problems, it won’t eliminate them.
“Most Class A motorhomes — except for higher-end coaches with air bags — rely on a leaf-spring suspension,” he said. “It’s really about the only component connecting the body to the chassis of the RV. And you have these outside forces working against the RV. Whatever road fluctuations the tires are hitting are moving the chassis under the RV, while this huge wind sail — there’s a tremendous amount of surface area to a Class A coach — is moving it independently of the chassis. So the driver, positioned well above the chassis, feels the wind push the motorhome one way or another — called body roll, or sway — and he reacts to it, instinctively steering in the opposite direction. He’s reacting to what he’s feeling. But it’s the upper part of the RV that’s affected the most; in fact, the chassis may not have even moved away from a straight line yet.”
Sway bars, he said, add a lot more stiffness between the chassis and RV “house” so they are more in synch with one another. “The driver isn’t counter-steering all of the time — the only time they need to make a steering adjustment is when the actual chassis moves the RV left or right.”
The size of the sway bar, Robinson added, is critically important.
“A typical motorhome sway bar is 1 1/8 inches to 1 1/4 inches in diameter,” he said. “Our sway bars are, at minimum, 1 3/8 inches, while most are 1 ½ inches to 1 5/8 inches in diameter — and on larger chassis we may go up to as much as 2 inches to 2 1/4 inches.
“That may not sound like a huge difference, but each 1/8-inch increase in diameter increases roll resistance — the sway control — by 30%. In most cases, our sway bars are 3/8-inch larger diameter than the OEM bar, so they provide more than a 100% increase in roll resistance (compared to the stock part). So, a sway bar will ‘fix’ the roll problem.”
As for the use of a steering stabilizer?
“One thing a steering stabilizer can do that no amount of sway control can accomplish is protect against blowouts,” Robinson said. “If a driver experiences a catastrophic front tire blowout, when the wheel hits that asphalt and digs in, it’s like throwing an anchor out on that side of the RV. The motorhome immediately tracks to that side — and that is a very dangerous thing. Products like our Reflex steering stabilizer absorb that immediate impact, so the steering wheel isn’t ripped out of the hands of the driver.”
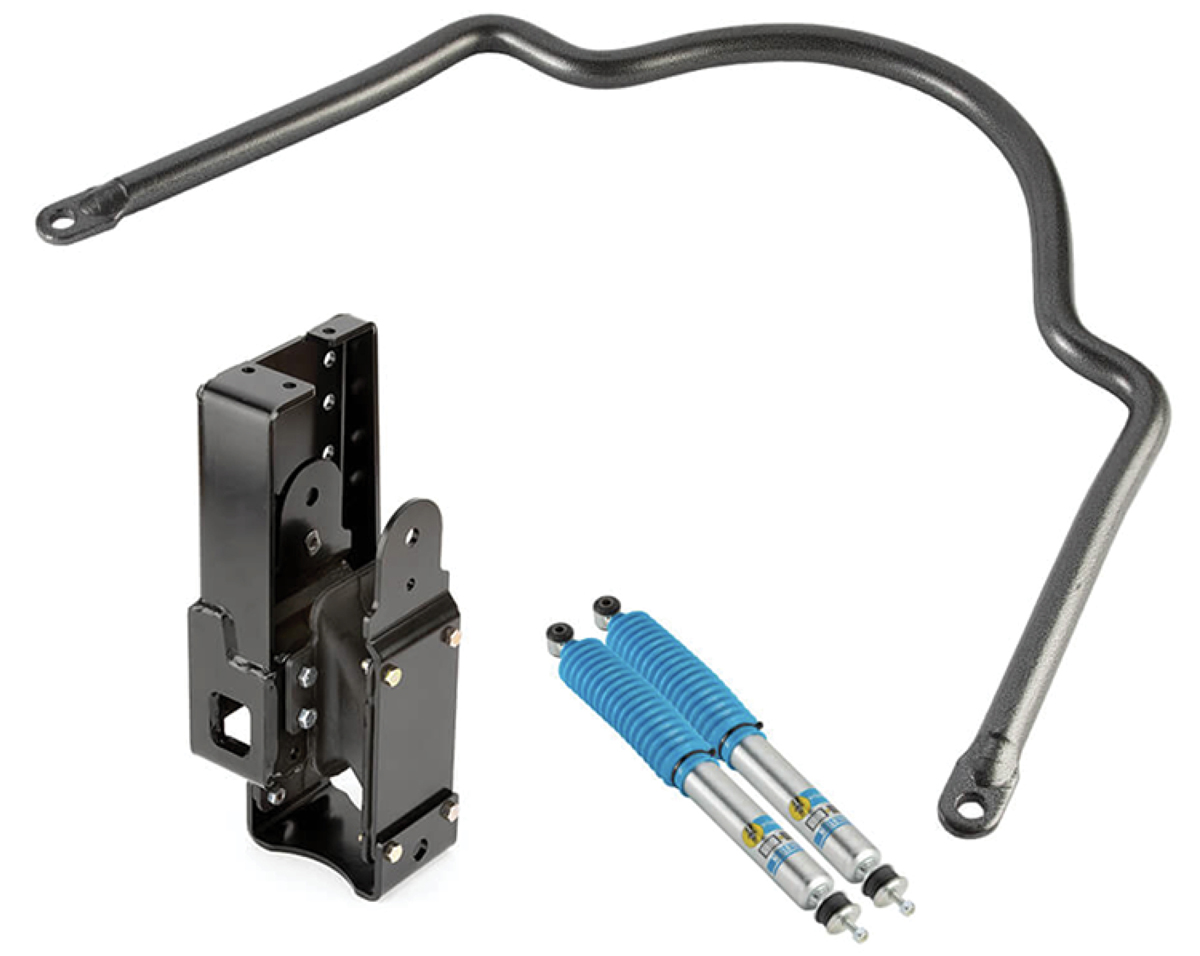
Designed to work in conjunction with a motorhome’s existing leaf spring suspension, the MORryde RS (for “rubber shackle”) suspension system replaces the stock leaf spring hanger (accomplished with either a grinder or torch) with a new MORryde-designed hanger. The second part of the suspension system is a unique spring carrier assembly that incorporates a double rubber sheer spring that provides up to four inches of suspension travel.
“It’s a double rubber shear spring that moves vertically, up and down, and works ‘in shear,’ which means the rubber doesn’t get stiffer with the more load you apply to it. What will happen is when the tires encounter a bump and go up, the vehicle leaf spring deflects that movement somewhat — then the rubber shear spring allows it to deflect even more.”
The RS suspension system — MORryde calls it an “airless” system because it provides for a smoother ride without the need for air bags — also provides different mounting options that allow the operator to choose between lower and higher riding heights. And, depending on the amount of added control an owner wants, the RS system can be acquired by itself or as part of MORryde’s RSX suspension system, which includes a heavy-duty sway bar and Bilstein shock absorbers. It’s available for an array of Class C coaches, with fitment also available for certain Class A motorhomes and even larger pickup trucks. A slightly different system, designed to perform in much the same way, is available for Ford Transit-based motorhomes (BRSC suspension system).
Travel Trailer & Fifth Wheel Upgrades
Remember earlier when we alluded to certain upgrades being well worth their small cost? One we had specifically in mind is the use of a heavy-duty shackle kit to tie together the leaf-spring suspension with equalizers on most travel trailers and fifth wheels.
“The standard in the industry is to use ¼-inch-thick brackets along with plastic bushings wherever there’s a spring ‘eye’,” explained Enfield. “What happens over time is that bushing wears away, which then causes the steel bolt to rub on the shackle bracket. This can progress to the point where the bracket elongates and finally snaps — leaving the customer on the side of the road.”
This is a simple fix. MORryde has engineered a heavy-duty shackle bracket kit replacement kit that upgrades every part: the bracket thickness is doubled, to ½-inch; the plastic bushings are swapped out for bronze units; and the standard bolts are replaced with greaseable “wet” bolts. (Similar kits also are available from Lippert, Dexter Axle and others.)
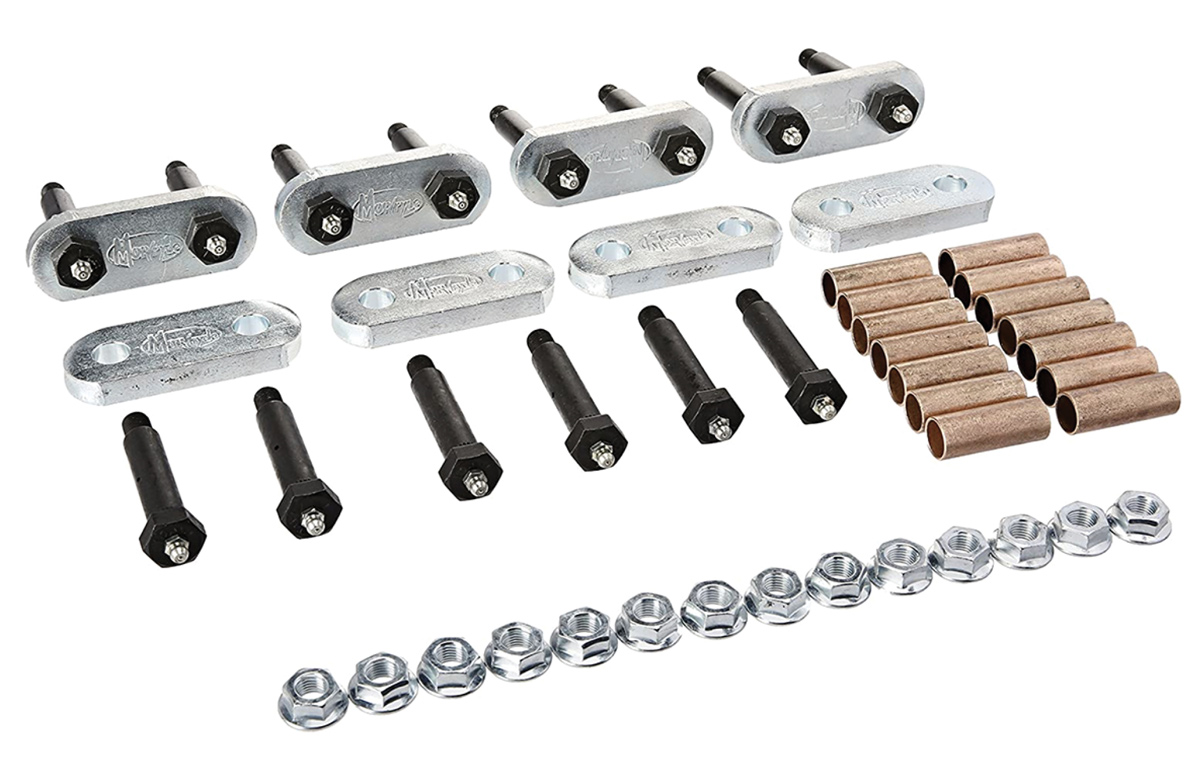
“We did a simulated 100,000-mile durability test of our kit, without lubricating it,” said Enfield. “The bronze bushing wore because it had no lubrication, but the ½-inch bracket did not wallow out (become misshapen due to friction). So while all the parts, properly maintained, work to further increase durability, the real lynchpin is the ½-inch bracket.”
Given that the retail cost of a dual-axle kit is only around $100 or so, and the propensity for the shackles to wear, it begs the question: why aren’t RV manufacturers upgrading the shackles at the factory?
“We are seeing more manufacturers go to it,” said Enfield. “Years back, Keystone was one of the first with its Montana (fifth wheel). Today, Grand Design and Jayco use it. When Alliance RV launched, its company executives did a lot of research with consumers and focus groups and found that there was a lot of concern about the RV foundation, so they went with our series 3000 equalizer and heady-duty shackle kit. So, there is a growing awareness — and manufacturers are responding to it.” In fact, Grand Design announced in late January it would go so far as to offer MORryde’s IS Independent Suspension system as an option on new Solitude and S-Class fifth wheels (a complete installation of the system, installed by Henderson’s Line-Up Brake & RV on a Solitude ST310GK fifth wheel, can be found elsewhere in this issue).
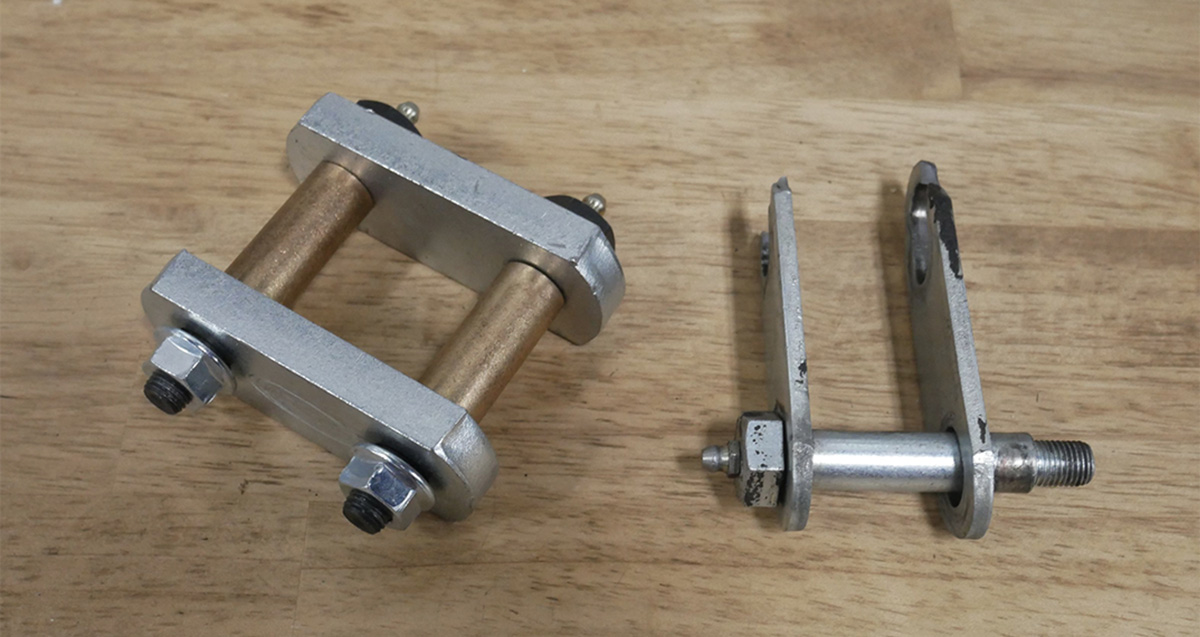
“Typically, leaf springs have about 2 inches of travel, from unloaded to maximum travel,” he said. “To protect the foundation and everything inside, you want to improve the travel of the suspension system — but the traditional equalizer is just a steel rocker; it doesn’t provide additional vertical travel. What an RV owner can do, though, is replace that stock part with an upgraded rubber equalizer.”
As Enfield related, equalizers the likes of MORryde’s CRE3000 and ALLTREK 4000 (as well as similar products from Dexter Axle and Lippert) combine rubber isolators with increased travel to help cushion the RV from road shocks.
“When the wheels go over a bump, you want them to have some ‘give,’” he said. “Otherwise, all that shock is transferred to the frame, side and everything inside the trailer. The replacement equalizer, he added, serves two purposes: by utilizing rubber as a cushion and increasing travel, it improves the RV’s structural strength and, by absorbing harsh inputs from rough roads, improves performance. The main difference between MORryde’s equalizers, he added, is travel: the CRE3000 provides for 3 inches of additional suspension movement, while the ALLTREK 4000 allows for 4 inches.
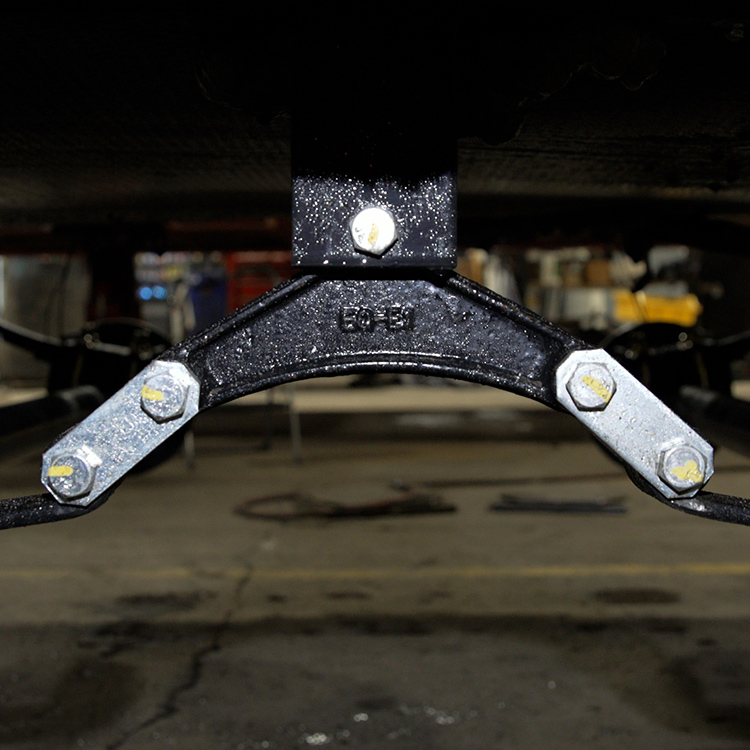
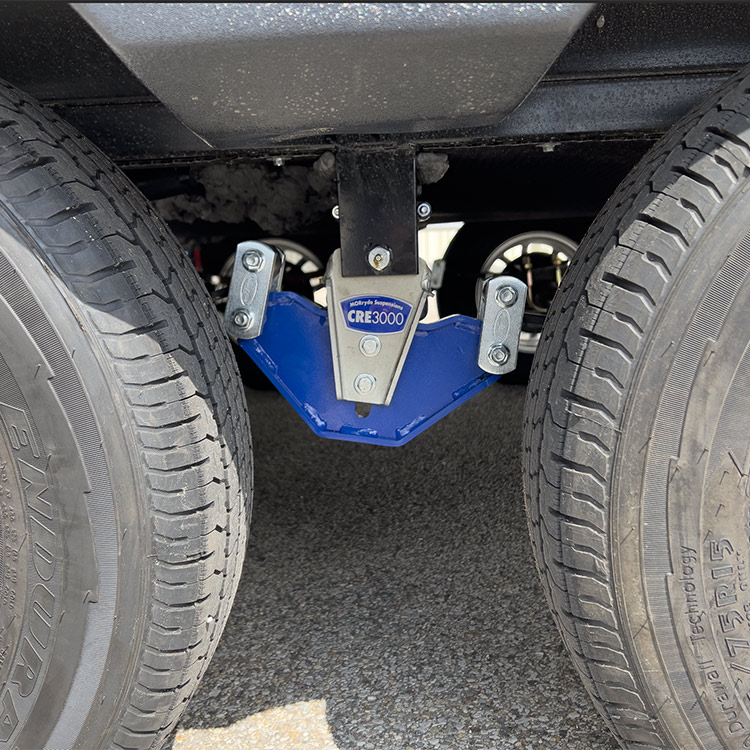
“How many cars are built today without shock absorbers?’” he asked hypothetically. “The answer is ‘none’ — because no one would buy them without shocks. It’s just terribly uncomfortable to ride in a vehicle without them.
“One ‘benefit’ that the RV industry enjoys is that no one really rides in a travel trailer or fifth wheel,” he told RV Enthusiast. “So, while experience has taught them the need to maybe wrap a bungee cord around the TV and make sure everything is off the countertops, they don’t realize how much abuse their trailer endures. It’s like a buckboard going down the road, but because they are towing it rather than riding in it, they don’t know just how rough the ride is.”
In fact, Robinson added, Roadmaster actually put sensors in travel trailers and fifth wheels and took them on a road course to measure the road’s impact on the RV.
“In terms of a Richter scale, the average impact was the equivalent of about a 3.2 earthquake going on inside the RV,” he said, “and that’s the average. Hit a pothole or speed bump, and it spikes.”
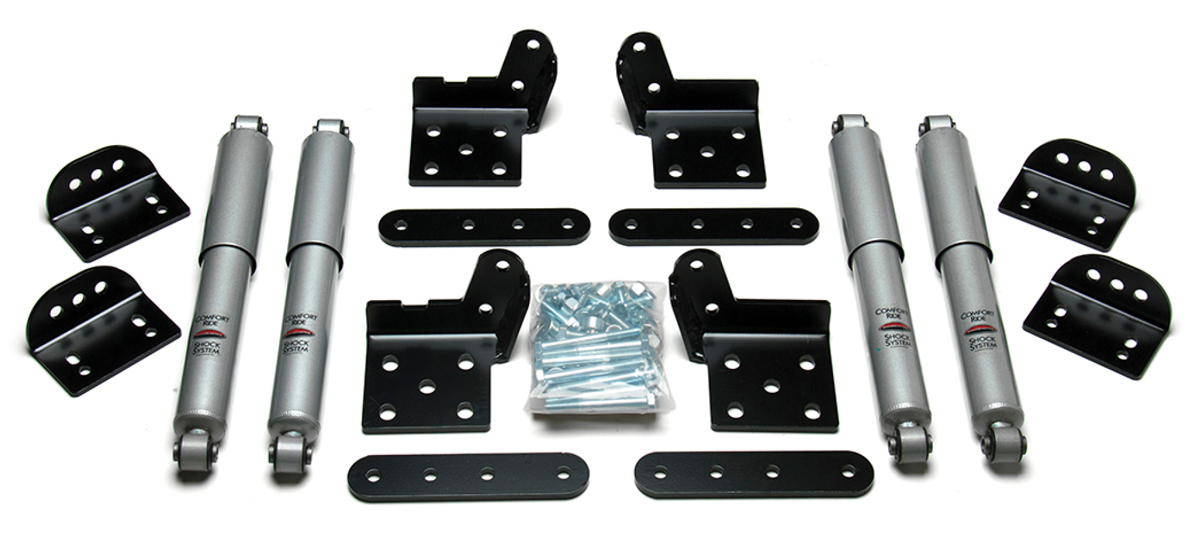
To counteract those forces, Roadmaster developed its Comfort Ride system, which can incorporate just its shock absorbers or in conjunction with “slipper” springs — essentially, leaf springs with one end curved (instead of a closed “eye”) to allow it to ride on a roller assembly within the Comfort Ride spring box. The complete package of shocks and springs (evaluated in the July 2021 issue of RV Enthusiast, see “The Bucking Stops Here”) provides impressive gains in control, but can also be budgeted for separately. As Roadmaster notes on its website, however, “Ride quality is significantly improved when both the slipper spring system and the shock absorbers are used in tandem.”
Roadmaster’s standard shock kit, meanwhile, is for a tandem-axle trailer, including everything needed to add four shocks, and is available for 2 3/8-, 3-, and 3 ½-inch diameter axles. (Here’s a tip: If the axle is missing an identification tag with axle capacity and diameter, an owner can either contact the RV manufacturer to decode the RV vehicle identification number to determine axle diameter/capacity, or just measure them. A 2 3/8-inch-diameter axle has a circumference of approximately 7 ½ inches; the circumference of a 3-inch or 3 ½-inch axle is about 9 ½ inches and 11 inches, respectively.)
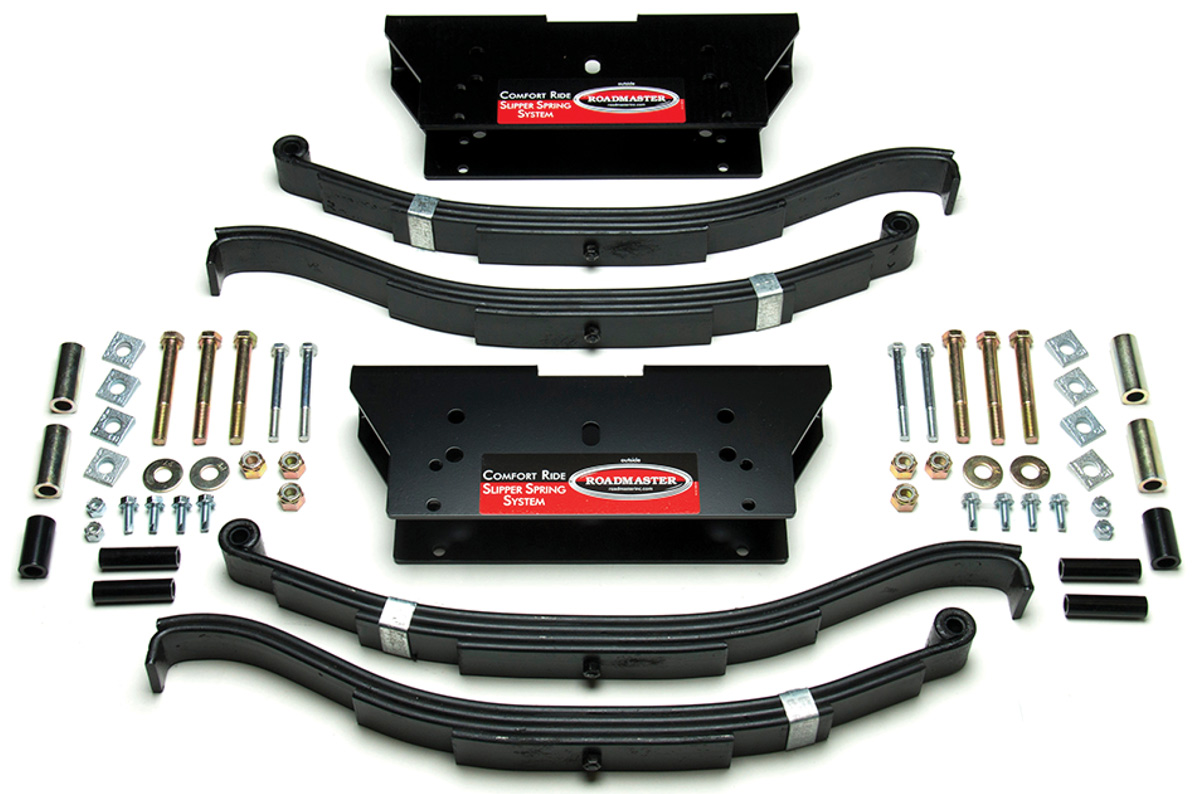
“It’s not as if we invented shocks,” he said. “It’s just that we figured out and patented a way to install them. One reason why trailers don’t have shocks is a lack of room to mount them. We developed adjustable mounting brackets that install vertically at a 15-degree angle. This also helps absorb sway. Bigger travel trailers and fifth wheels have a really high center of gravity, so just like a big Class A motorhome they want to sway back and forth.”
By themselves, Robinson said the installation of shock absorbers reduces forces exerted on an RV by about 80%.
“Just like as when used on a car, the shocks are absorbing all that energy before it hits the frame of the trailer,” he added. “And, the RV isn’t telegraphing as many forces to the tow vehicle. It’s really amazing how much better a trailer tows after the addition of shocks.”
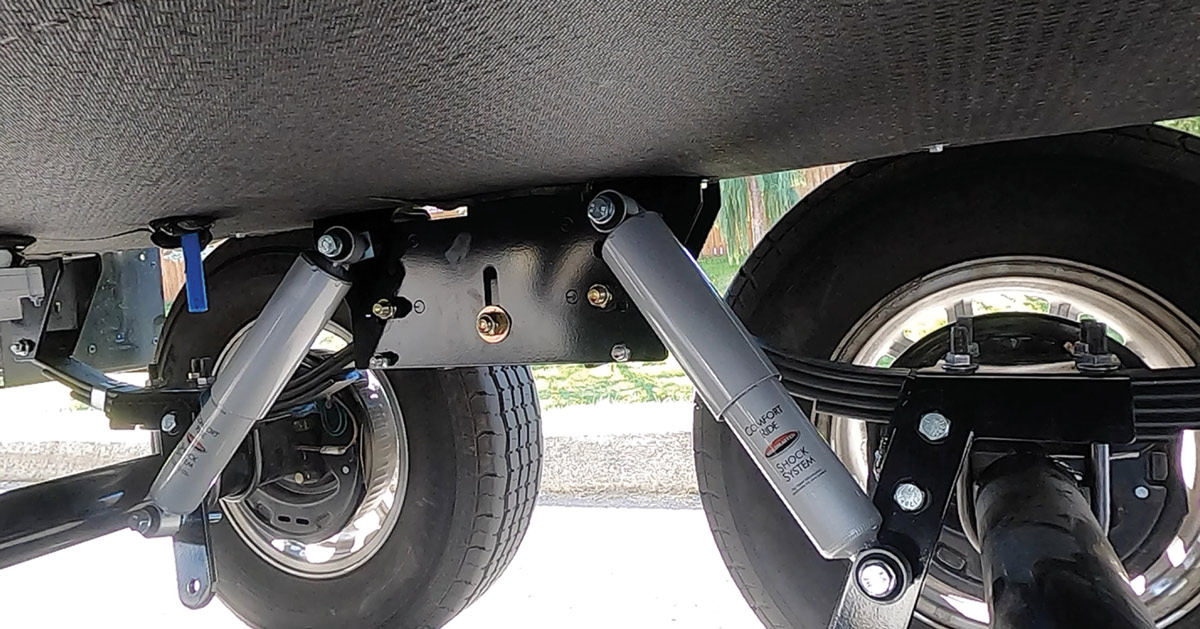
Like RVs, there’s a suspension solution for every budget.
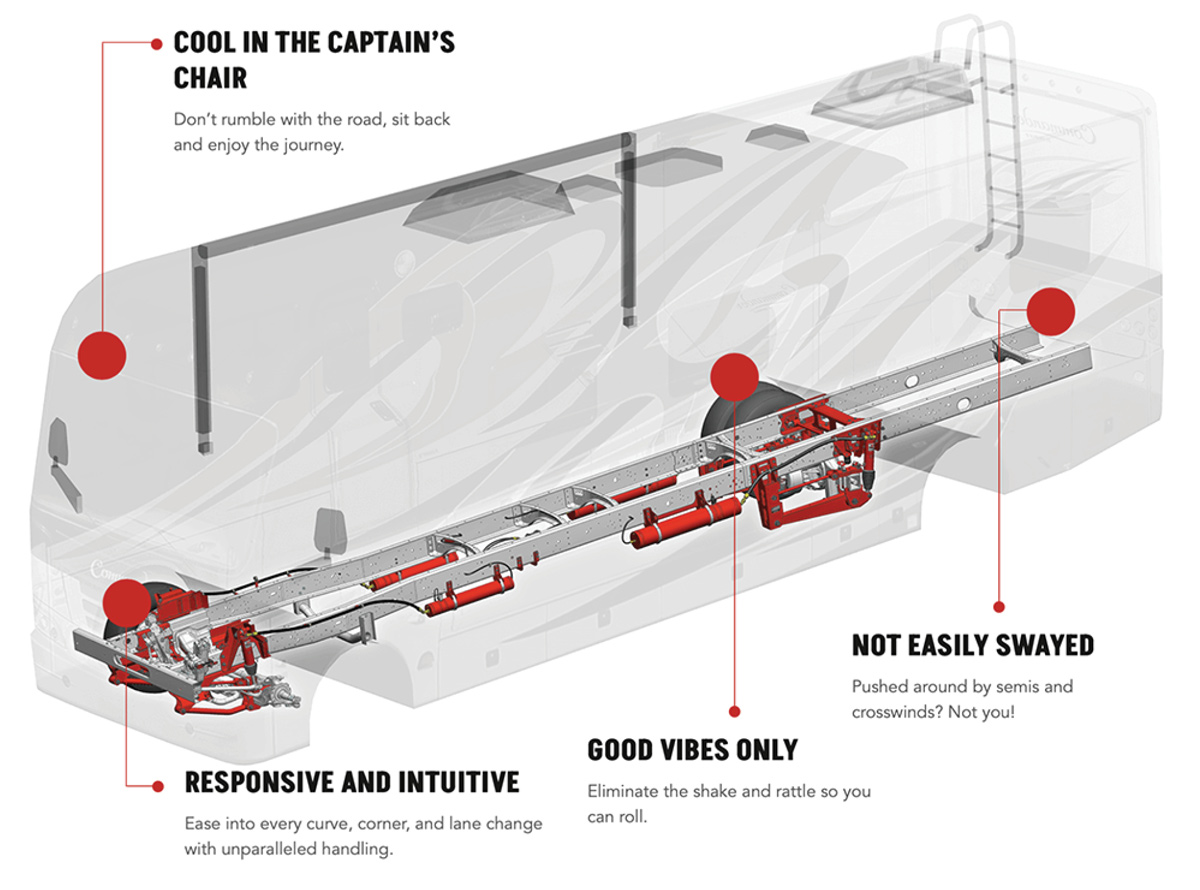
The “liquid” in the LiquidSpring (liquidspring.com) system is silicone-based and compressible under high pressure. Struts (a piston in a cylinder) replace the steel leaf springs. Instead of leaf springs flexing and loading under varying road conditions, the silicone-based liquid is compressed at a variable rate determined by an onboard computer that analyzes suspension movement in milliseconds and changes pressures (2,200 to 4,000 psi) in the struts as road conditions vary. The liquid serves as load support as well as shock absorbing; hence the variability the system provides is a radical transformation of the stock suspension system.
Each wheel strut is connected by a high-pressure hose to a volume, and the pressure in that volume is controlled via another high-pressure hose to the control module. The 12-volt-DC-powered module includes a high-pressure pump, computer-controlled valves and a reservoir for the compressible liquid. Pressure in each strut is controlled individually and instantaneously by the module based on data from height sensors at each wheel and a steering sensor. It adds up to an all-wheel variable/adaptive suspension.
Granted, this is neither a quick nor inexpensive transformation — but it is perhaps the best motorhome suspension available.
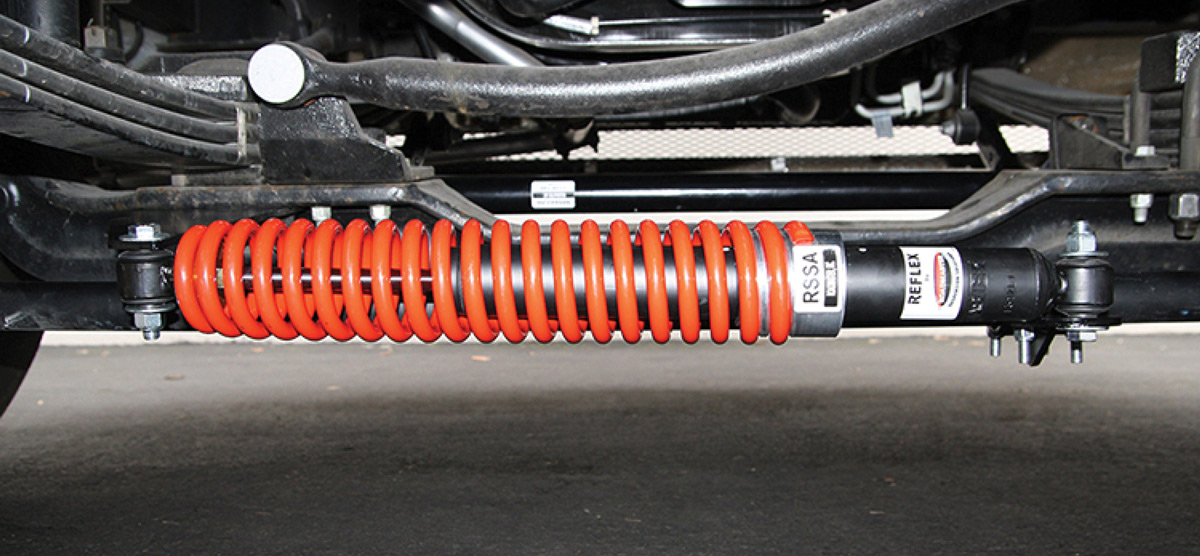
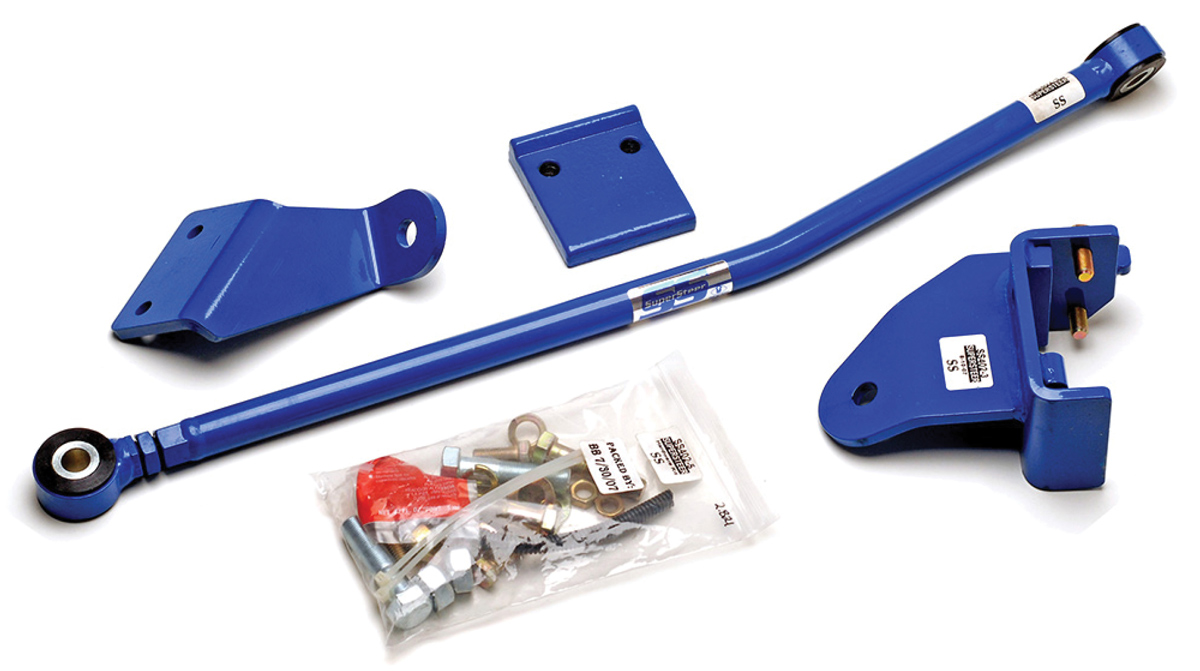
A rear trac bar is one of the better things you can add to a Class A or Class C motorhome suspension — particularly those with a lot of rear overhang. The bar bolts to the rear axle at one end (the mounting point depends on the application) and to the frame at the other along the same plane, preventing the axle from moving from side-to-side. With the rear axle rigidly located, steering input is dramatically improved. SuperSteer Parts (supersteerparts.com) and Ultra RV Products (ultrarvproducts.com/) both offer kits for a wide range of GM and Ford gas-powered motorhome chassis.
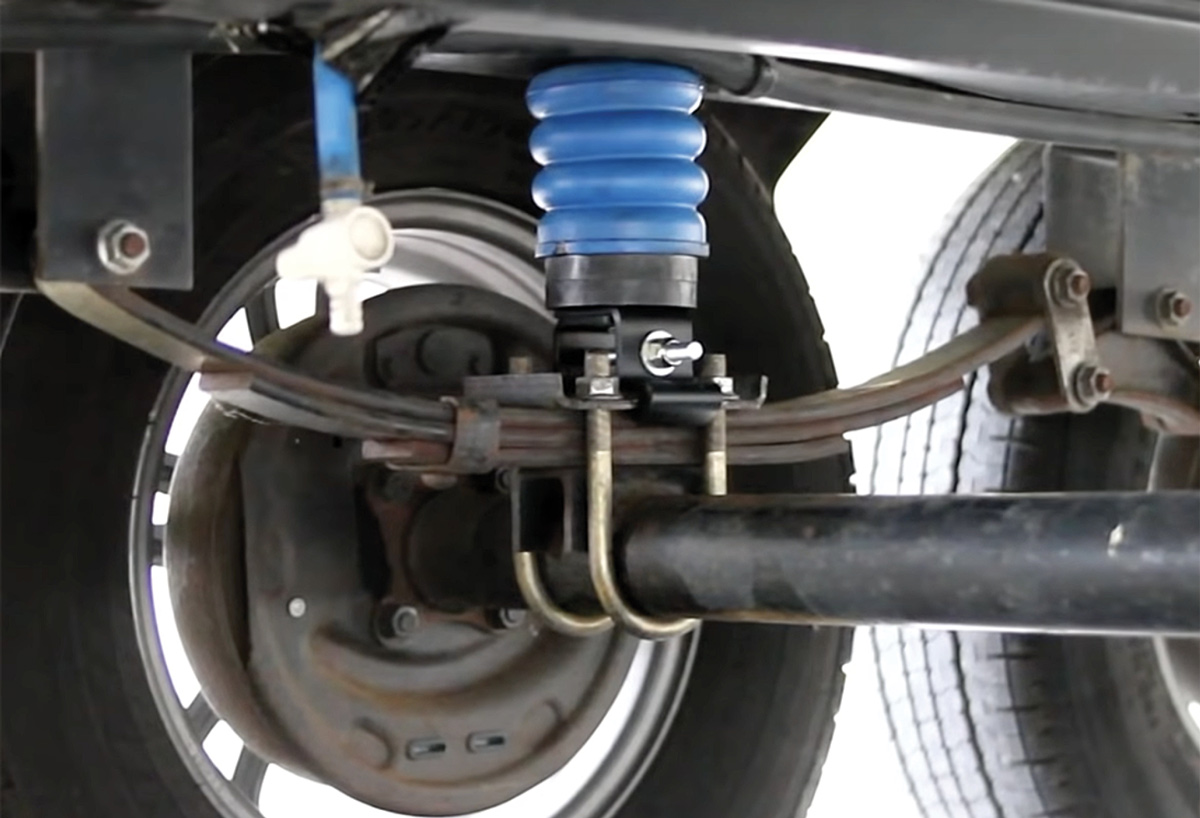
SumoSprings (superspringsinternational.com/sumosprings/) are available in two densities for towable applications: “Blue” SumoSprings are designed for trailers with gross axle weight ratings (GAWR) of 3,000 to 5,000 pounds, while “Black” springs are for GAWRs of 5,000 to 8,000 pounds (superspringsinternational.com/trailer-sumosprings/). There also are applications for motorhomes and tow vehicles — SumoSprings are, in fact, standard equipment on units from a number of RV manufacturers including Winnebago, Tiffin, Coachmen, Thor Motor Coach, PleasureWay, Roadtrek and Brinkley RV. Aftermarket kits are relatively inexpensive, available for over-axle and under-axle leaf-spring configurations and can be installed in about 30 minutes.