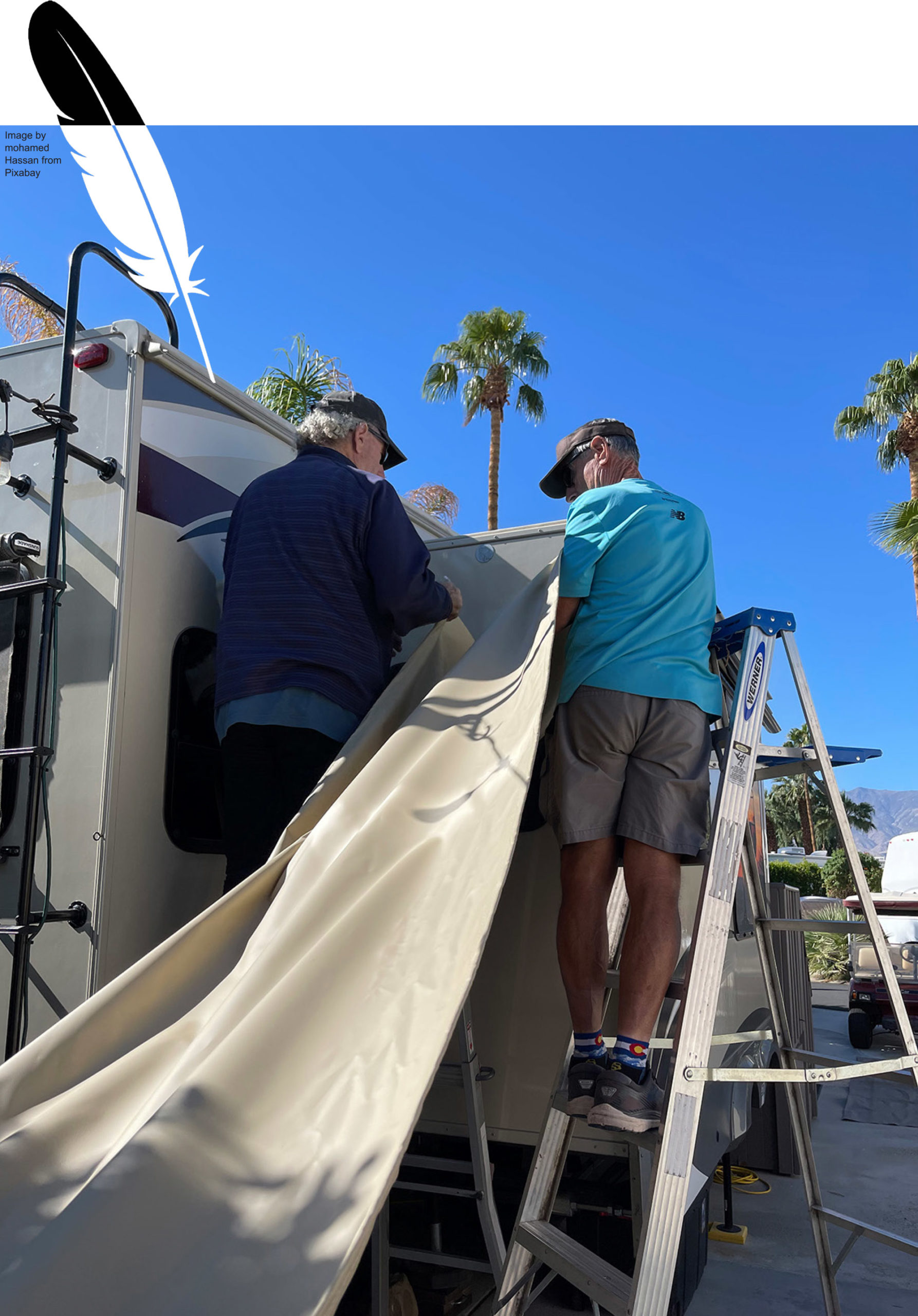
lide-out toppers play an important role when it comes to protecting an RV and are arguably one of the most abused accessories in the RV space. They shelter slide-out roofs from water intrusion and debris, quiet down the noise in rainstorms and generally improve the appearance of any RV. But slide-out toppers are always exposed to the elements unless they are retracted, and that’s only when the RV is in storage or on the road. The constant beating from strong winds will weaken the fabric — not to mention the cacophony of noise inside the rig — and eventually the material will tear, usually at the poly cord seam nearest the awning rail on the sidewall.
Last summer, the five-year-old acrylic fabric (the more expensive stuff) on all three slides in our fifth wheel were damaged beyond repair in a strong windstorm; within seconds, they were history.
Granted, over time any fabric exposed to the sun — and potential damage from branches and other debris that can collect on top when parked under trees — will weaken the material. Also, roller-tube springs that are not wound tight enough will allow the fabric to flop around, which will decrease longevity, as will ice, snow, hail and debris that’s allowed to roll up on the tube during retraction.
You get the picture: Slide-out toppers are subject to constant abuse.
Once we surveyed the damage, it was clear that the stitching holding the poly cord in place deteriorated much faster than the remainder of the fabric. When the seam on each topper finally let go, the fabric separated from the awning rails mounted to the sidewalls and retracted violently into the roller tube covers; some of the fabric also ripped in the process. The Carefree of Colorado Ascent slide-out topper hardware was still in good shape, however, so we elected to replace the fabric — which is not difficult, but is more complicated with this model.
The lack of available fabric during the current supply chain snafus and pandemic slowdown led us to Tough Top Awnings, a company that specializes in replacement fabric for patio awning and slide-out toppers. As we discovered, Tough Top’s fabrics are thicker and stronger and the company uses marine-grade thread (for boat sails) to sew in the poly cord. We figured (rightly, as it turned out) that if boat sails can take the punishment from the wind, the toppers would also fare well. Also, the company’s reputation is sterling and it has a five-year warranty, so we decided to give up on finding the same acrylic fabric used for the original toppers (that also matched the patio awning) and go with material from Tough Top in a beige color that was the closest match to the old toppers.
The first step was to determine the sizes of the toppers that were being replaced. The onus for this is on you, but the company’s website has explicit instructions on how to do measure properly, and easily accessible company personnel are well versed in this process being RV owners themselves. Although the videos on the website will show how to measure existing fabric, we varied the procedure by actually removing the roller tube and measuring the fabric on the ground. This gave us the opportunity to clean out the channel where the roller tube resides, which was filled with leaves, twigs and dirt. Again, the procedures will vary depending on the brand and model of slide-out topper.
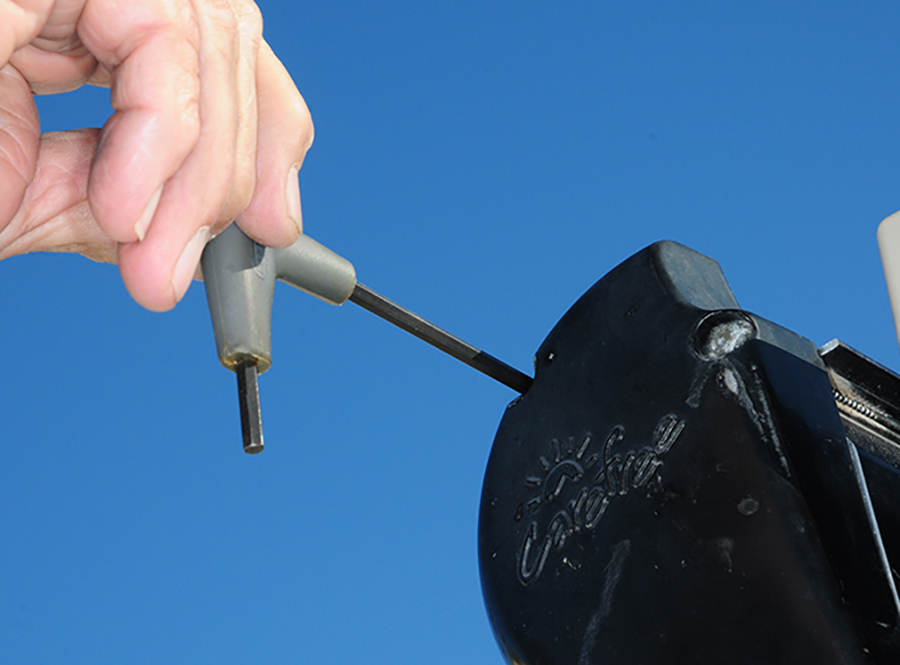
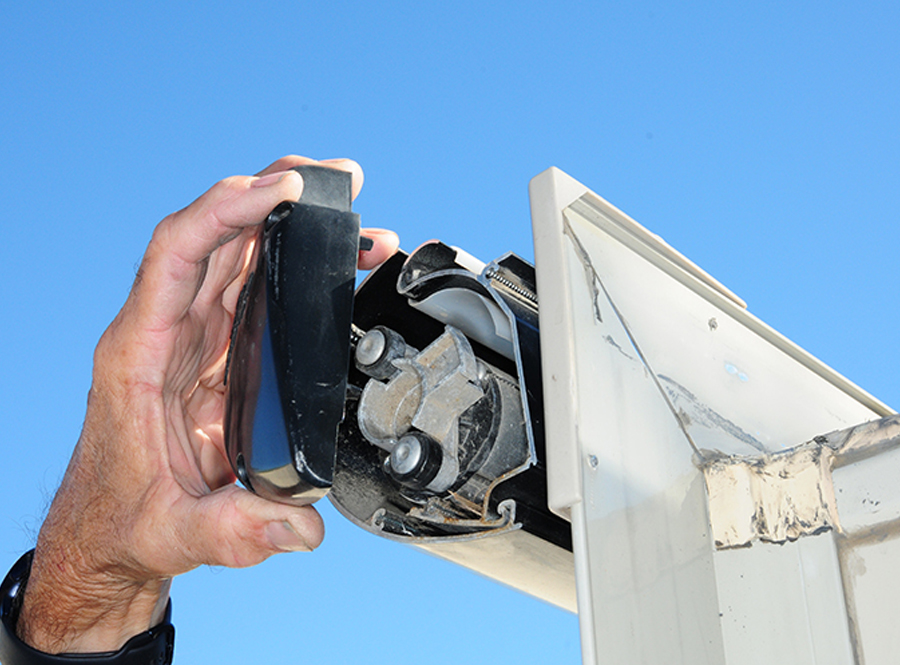
The next step is to remove the interior or exterior access panel for inspection. You’ll be looking for lint, dust and/or debris on the circuit board and blower wheel(s). Be careful not to disturb the wiring or compromise any of the components, which could lead to a furnace malfunction. Use a bright flashlight to inspect the interior of the partially hidden blower assembly to determine if a build-up of lint is present. With the help of a long-nose air nozzle, compressed air (at no more than 125 psi) can facilitate the removal of dust in the hard-to-reach areas. Avoid directing high pressure air toward the circuit board or other electrical components (play it safe and adjust air pressure to 20 psi when cleaning the board.)
Thoroughly inspect all of the wiring; it is not uncommon for rats or mice to chew through electrical insulation and conduit. Damage to wiring or other components may require the assistance of a certified RV technician.
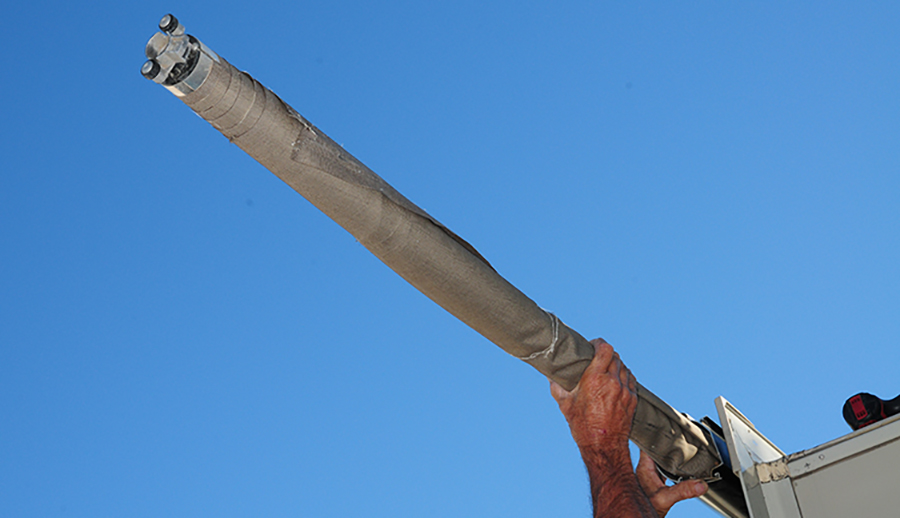
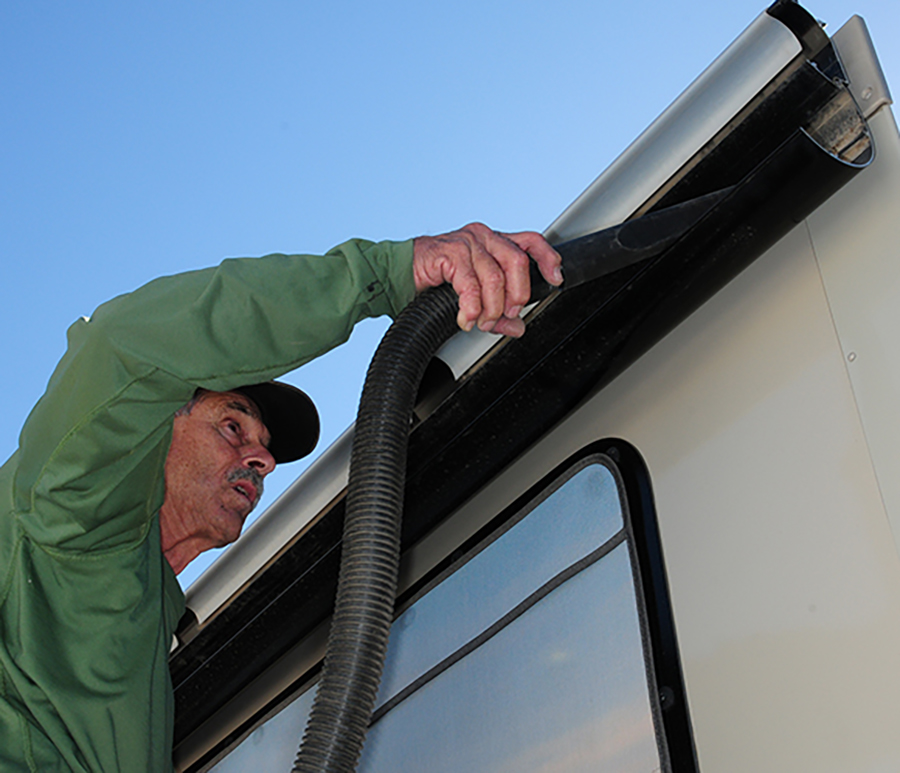

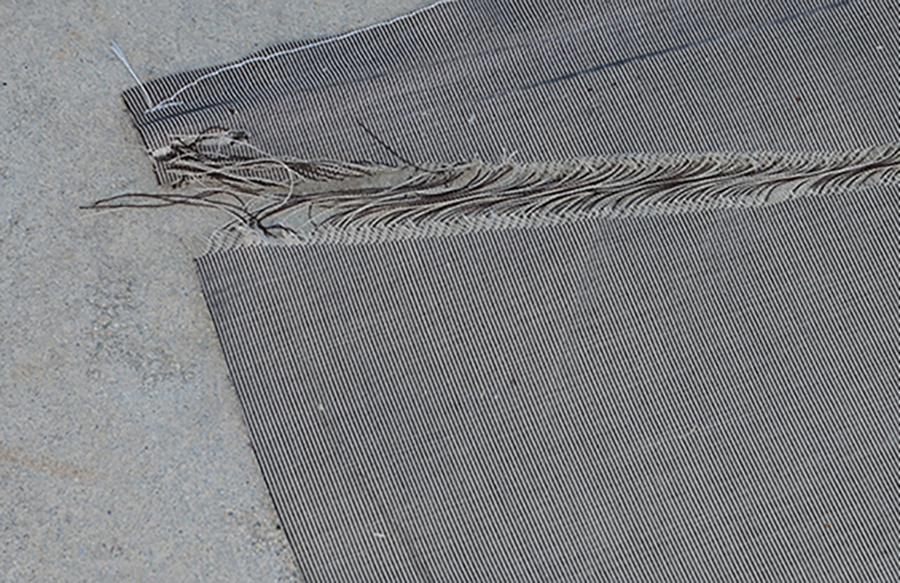
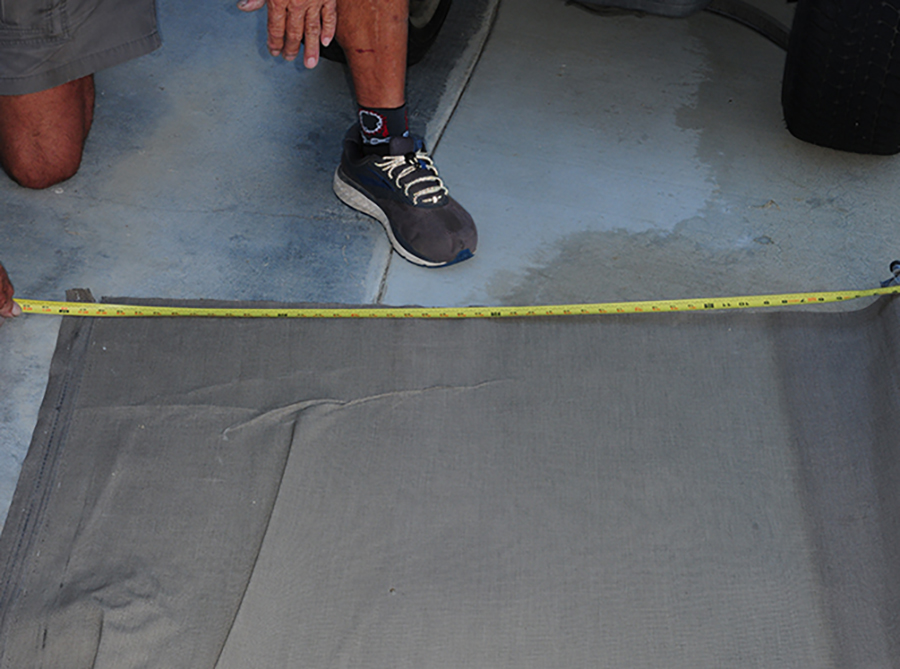
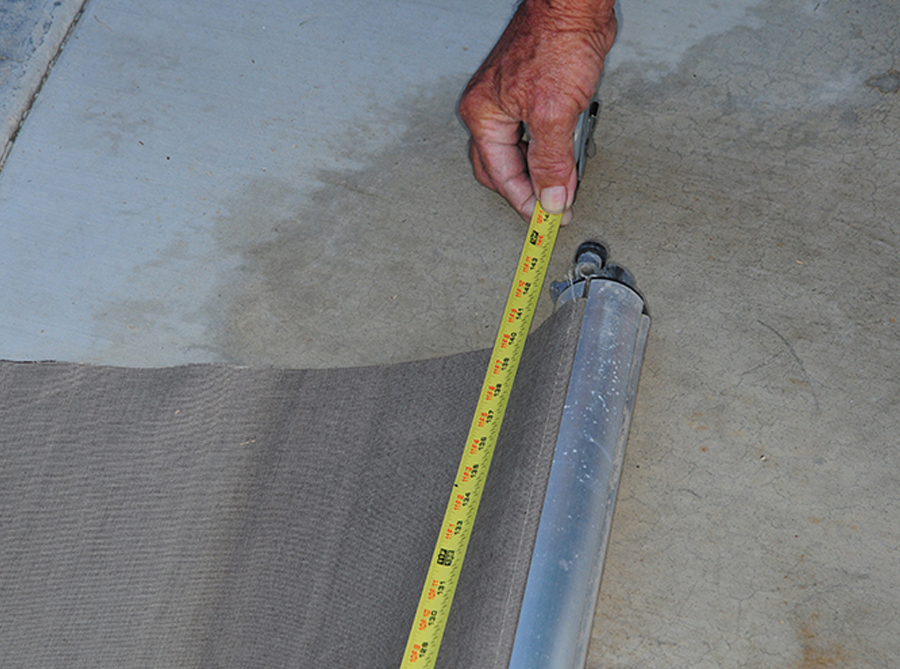
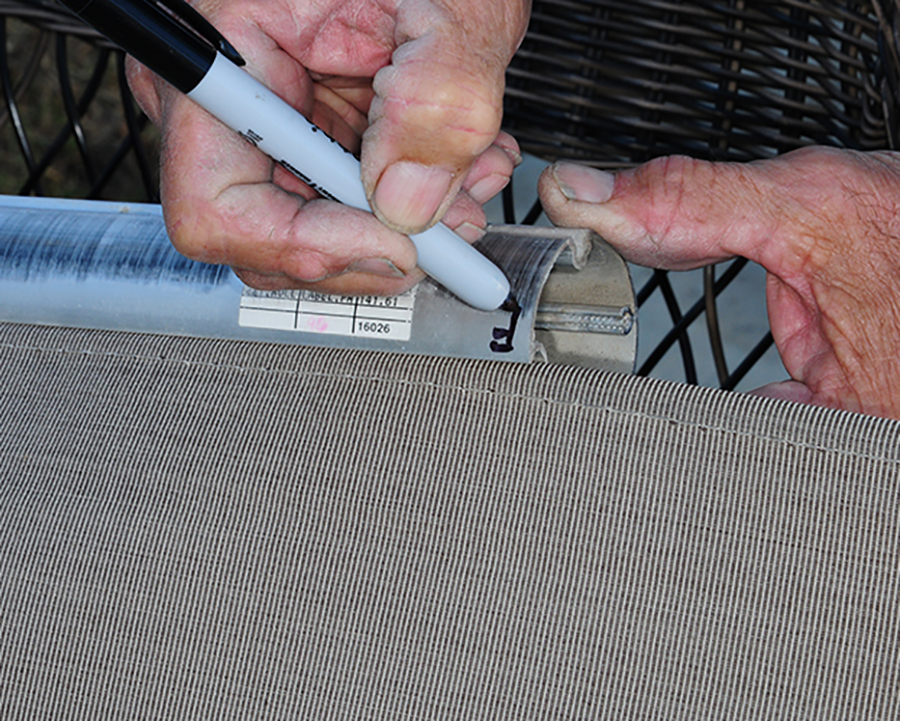
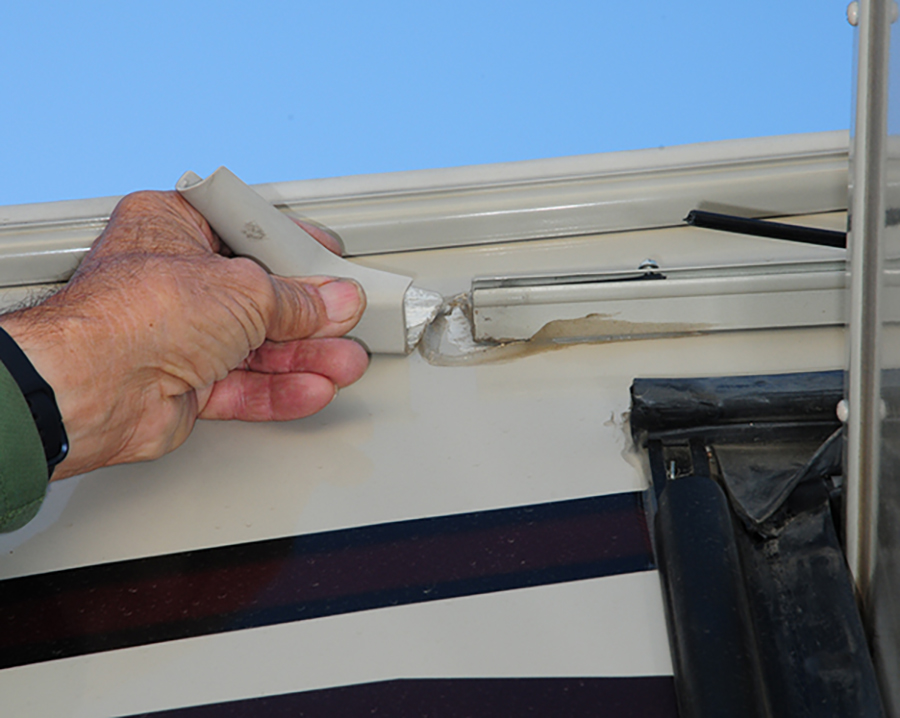
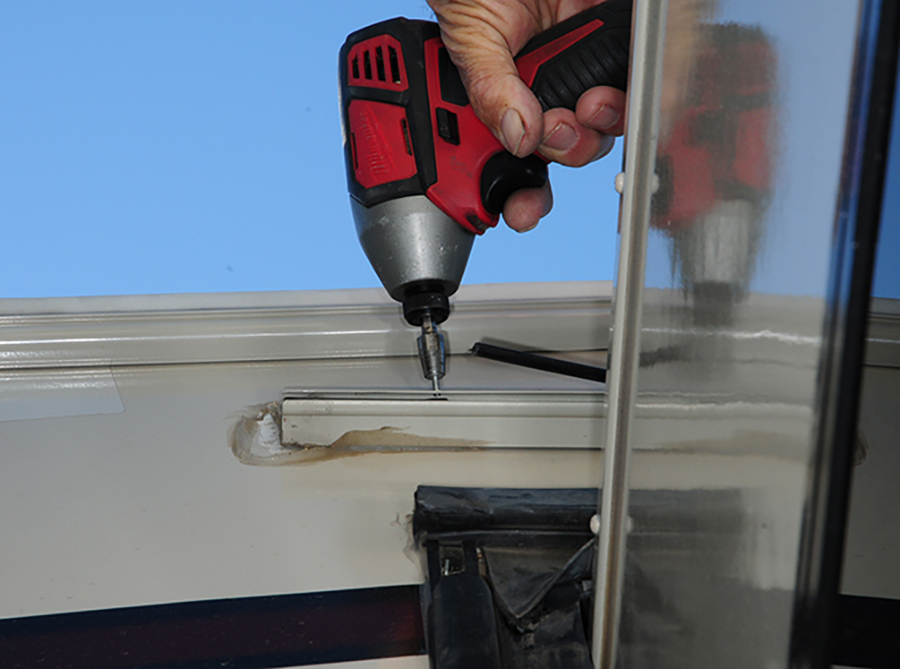
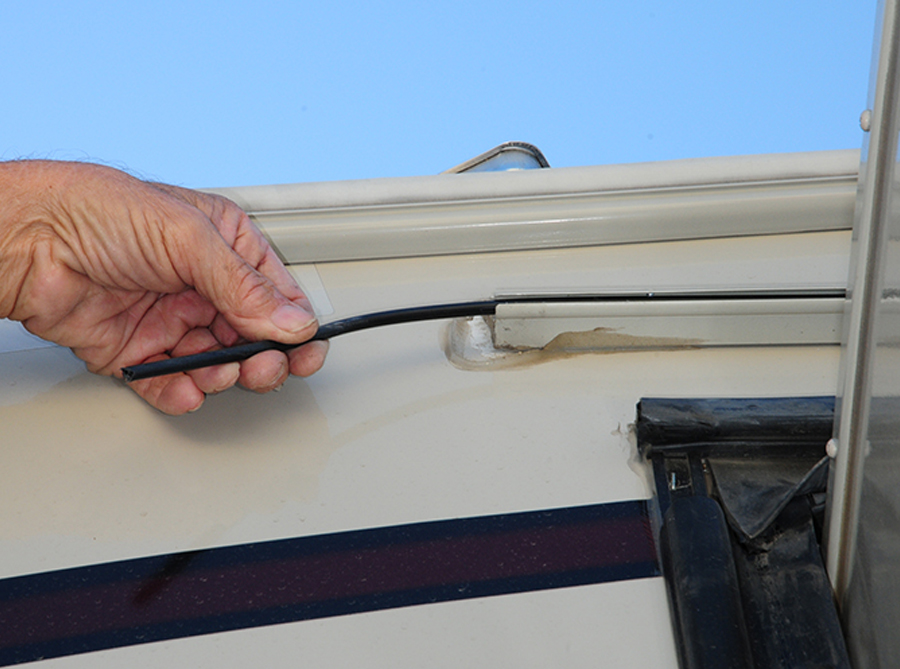
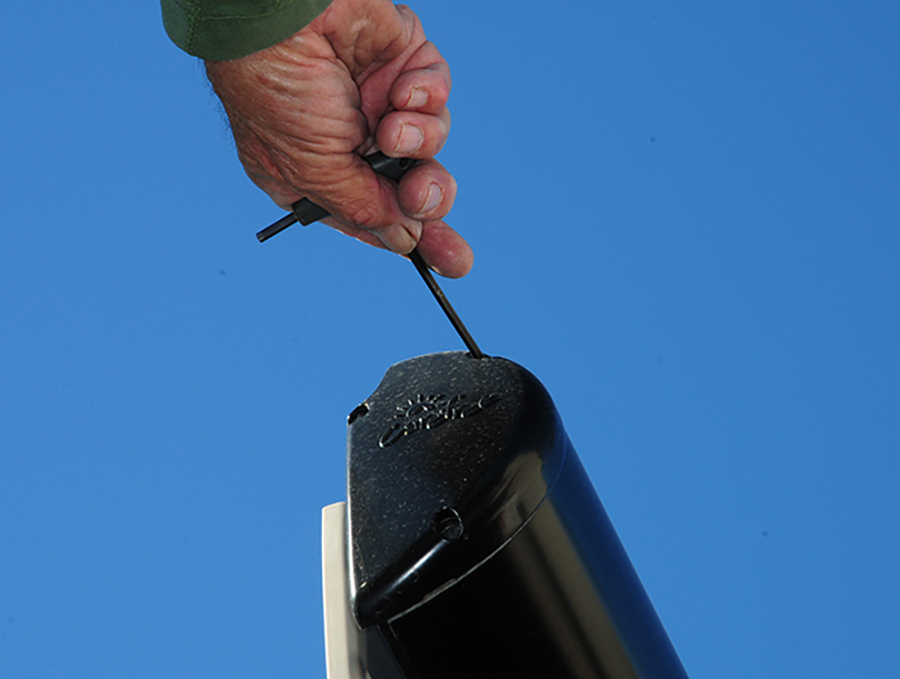
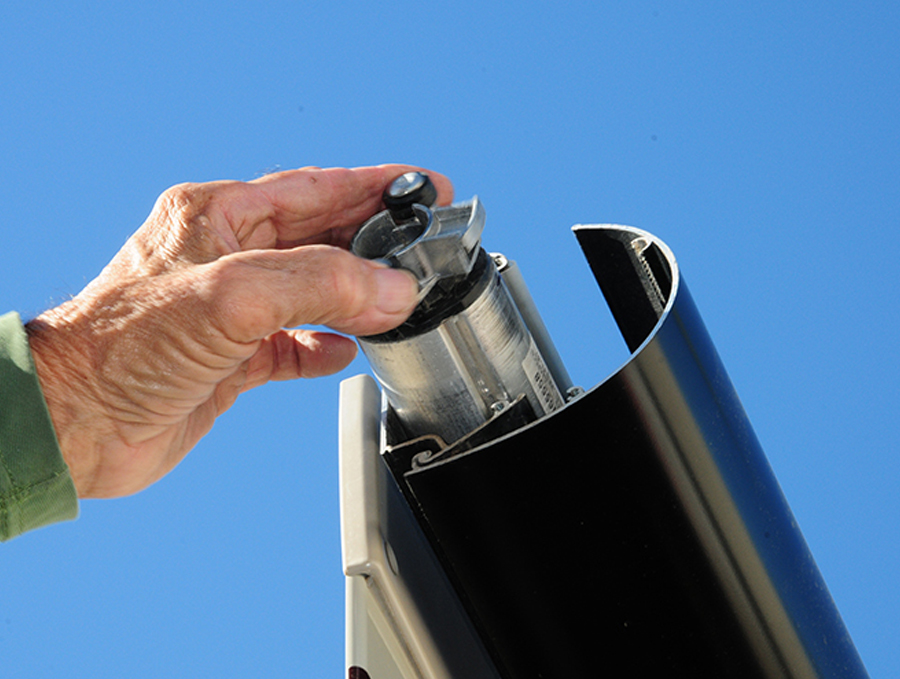
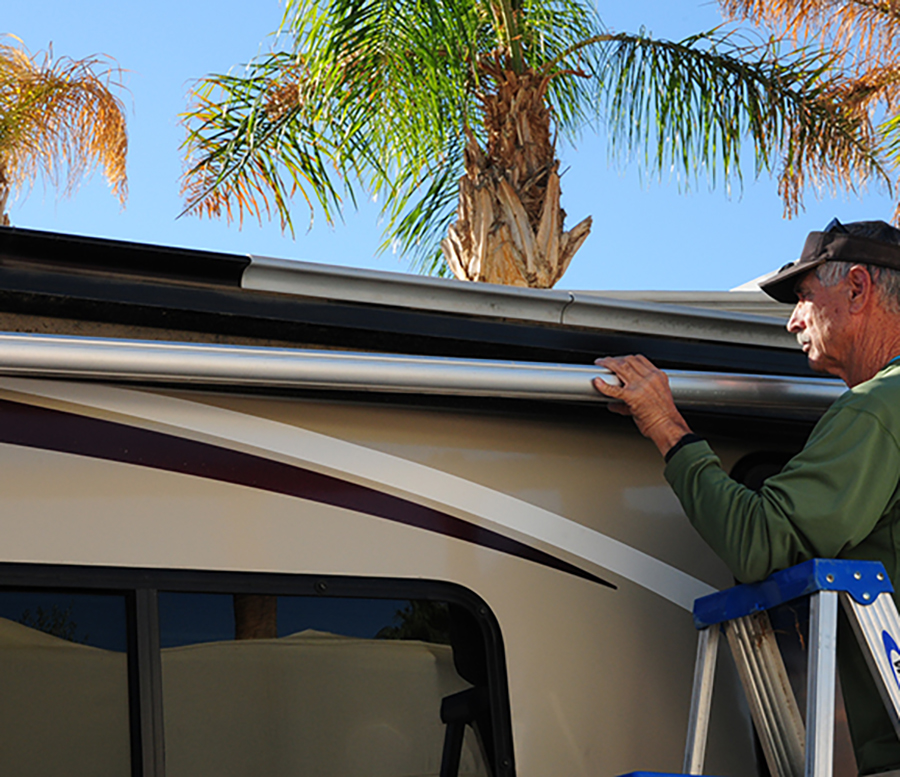
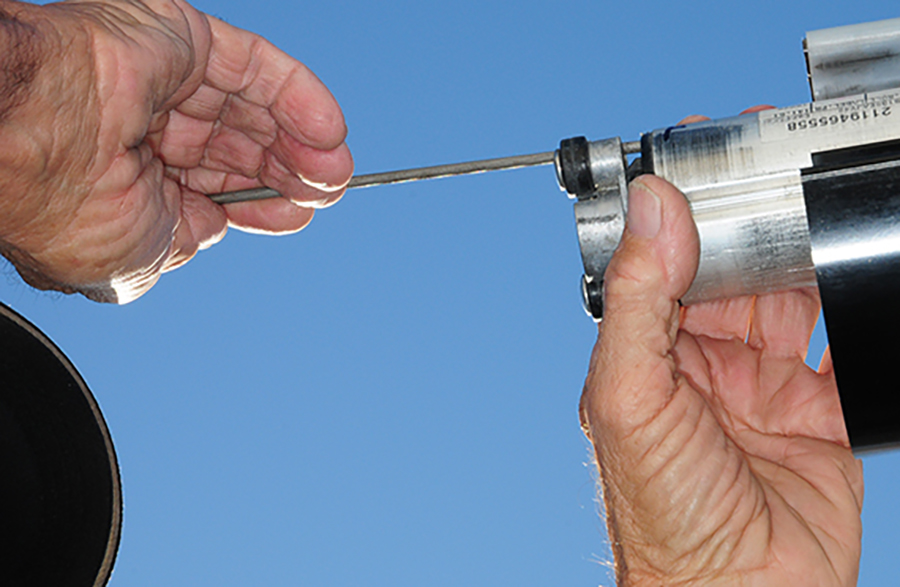
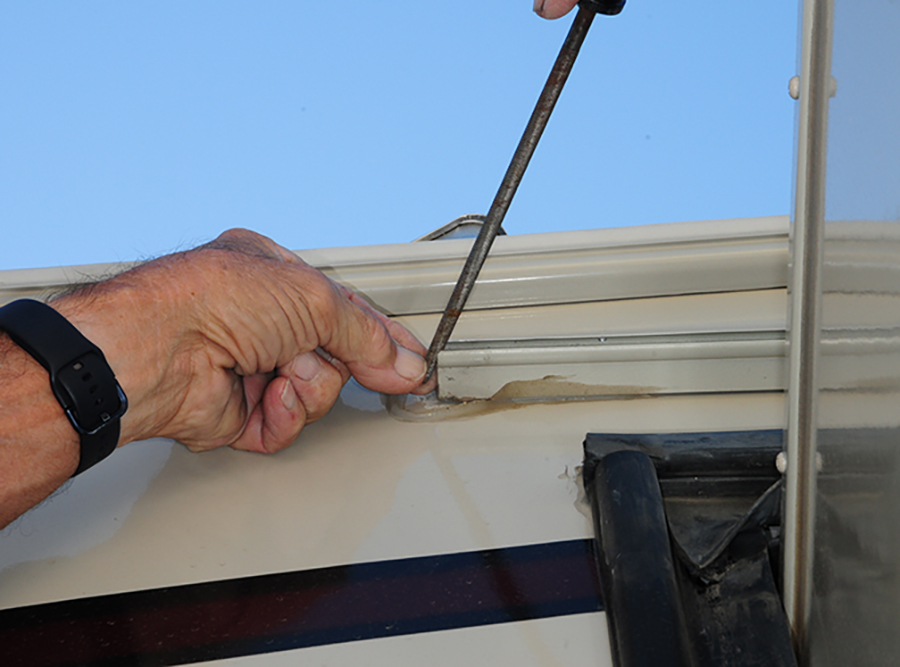
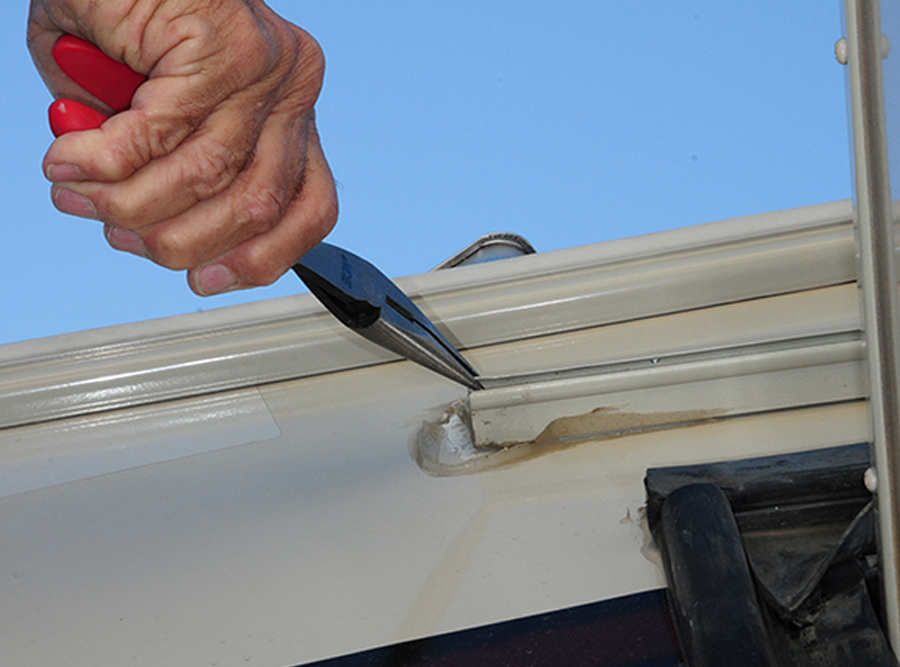
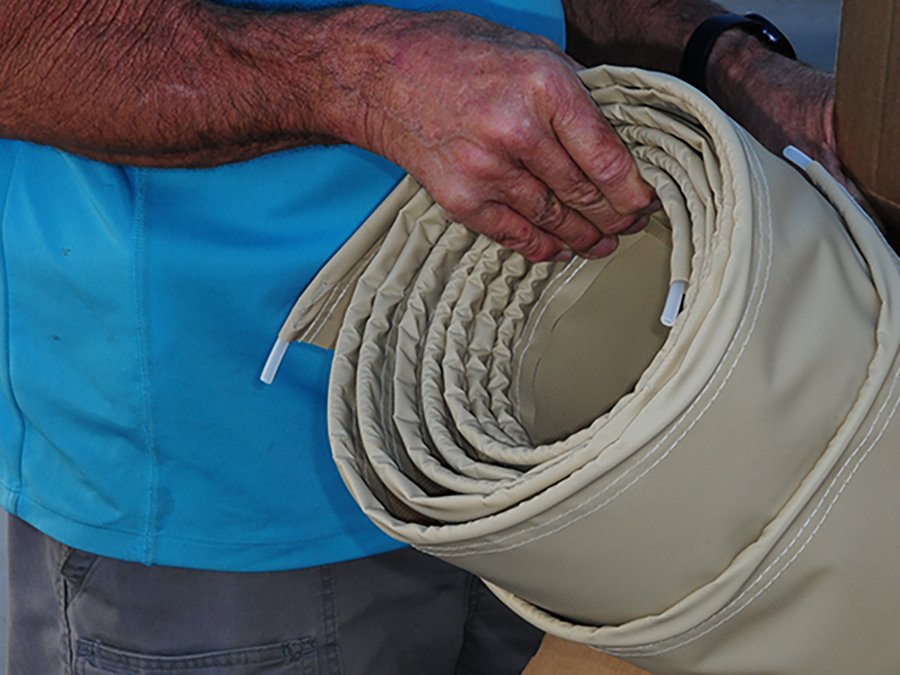
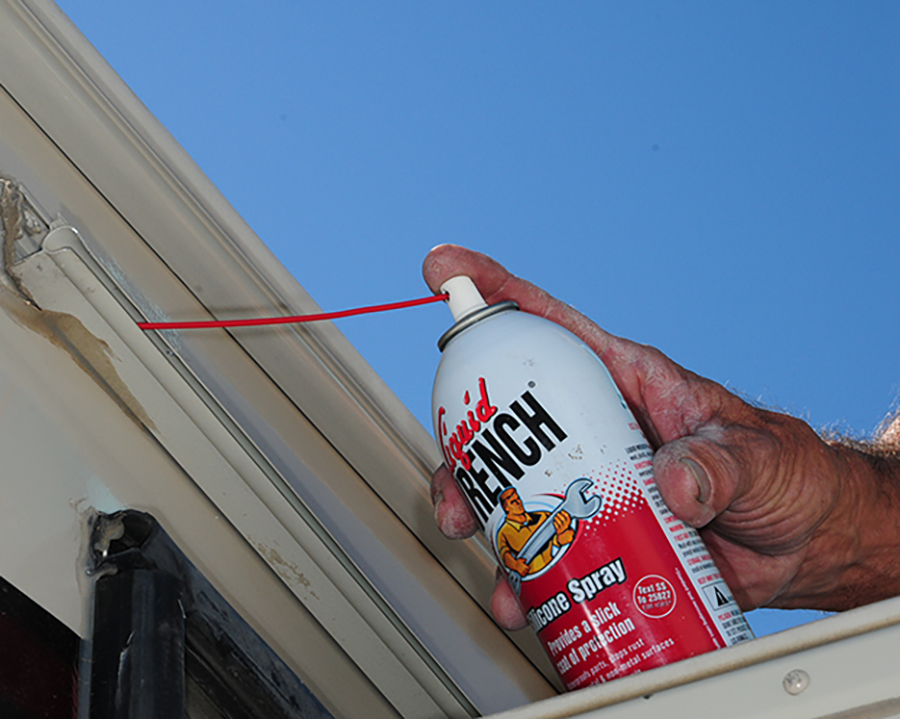
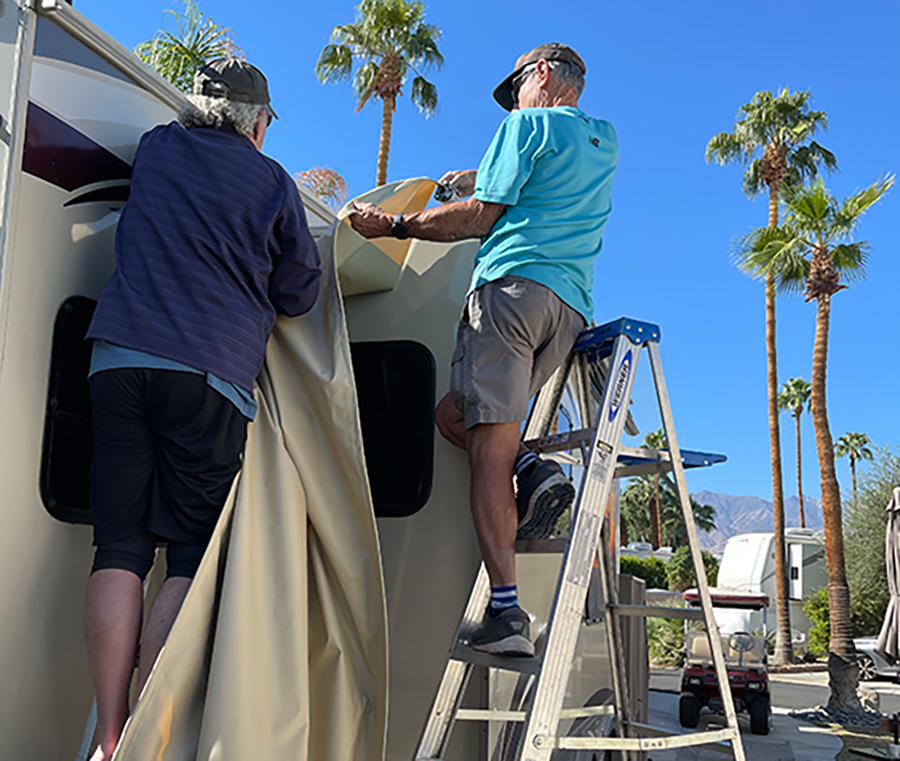
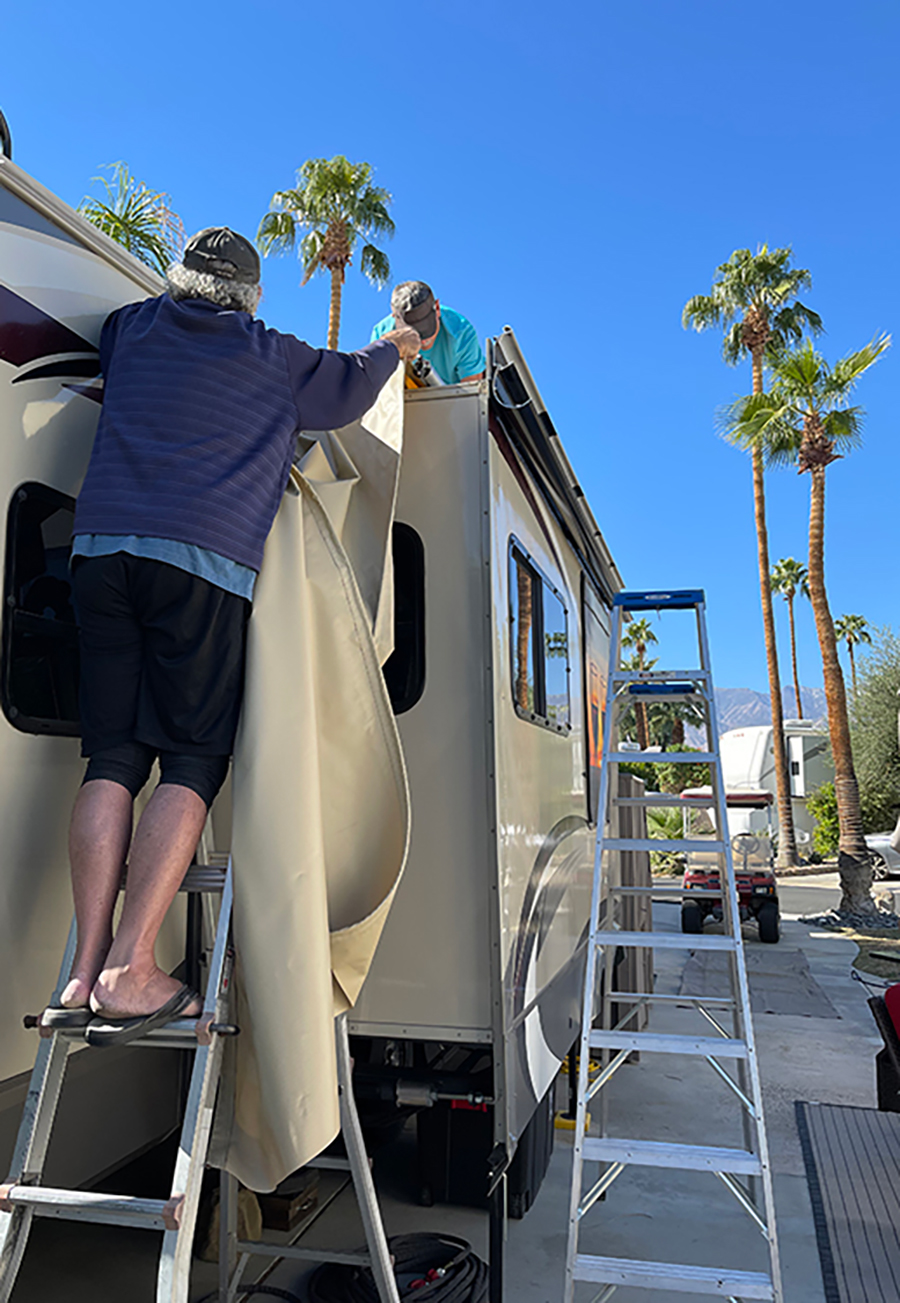
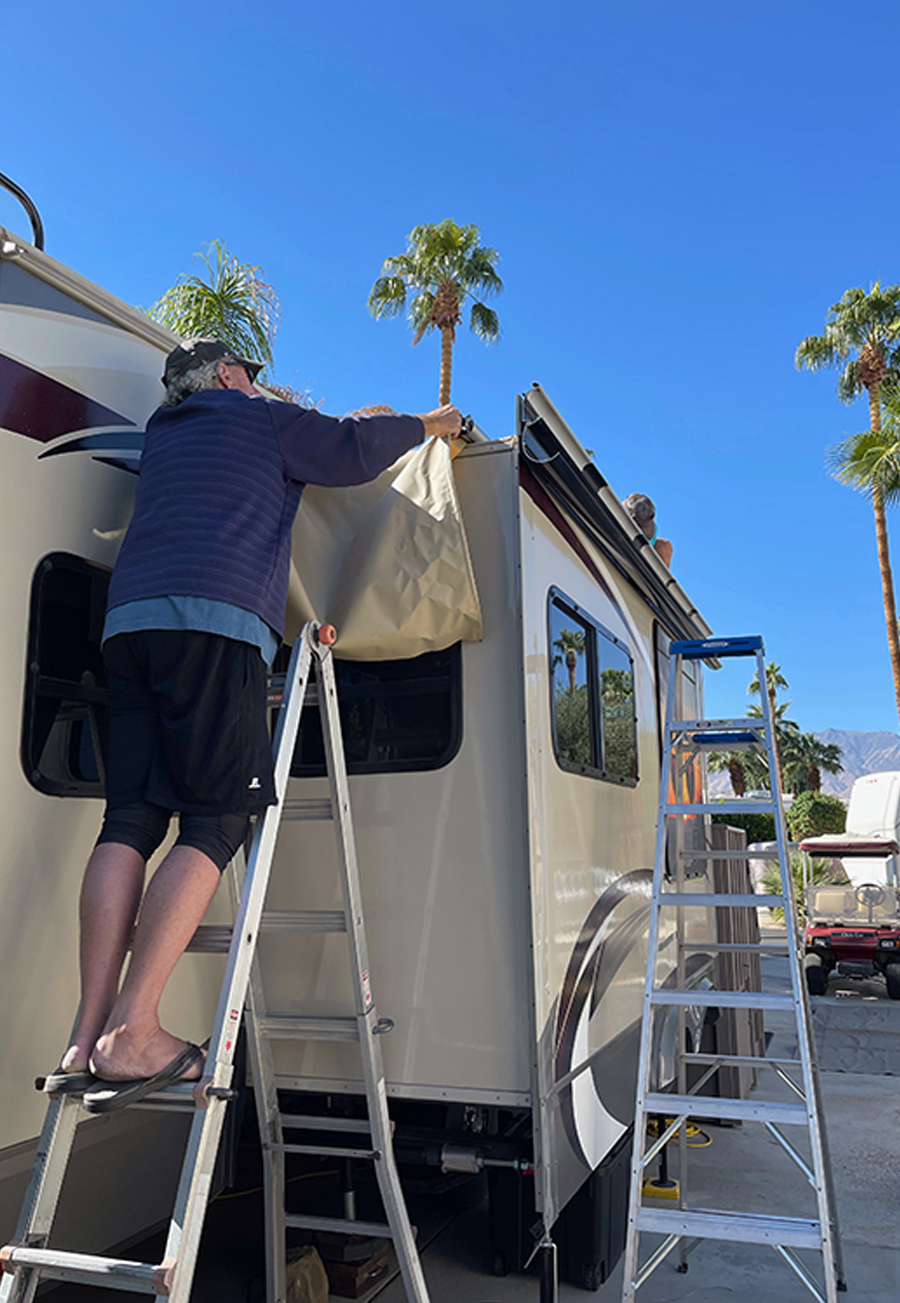
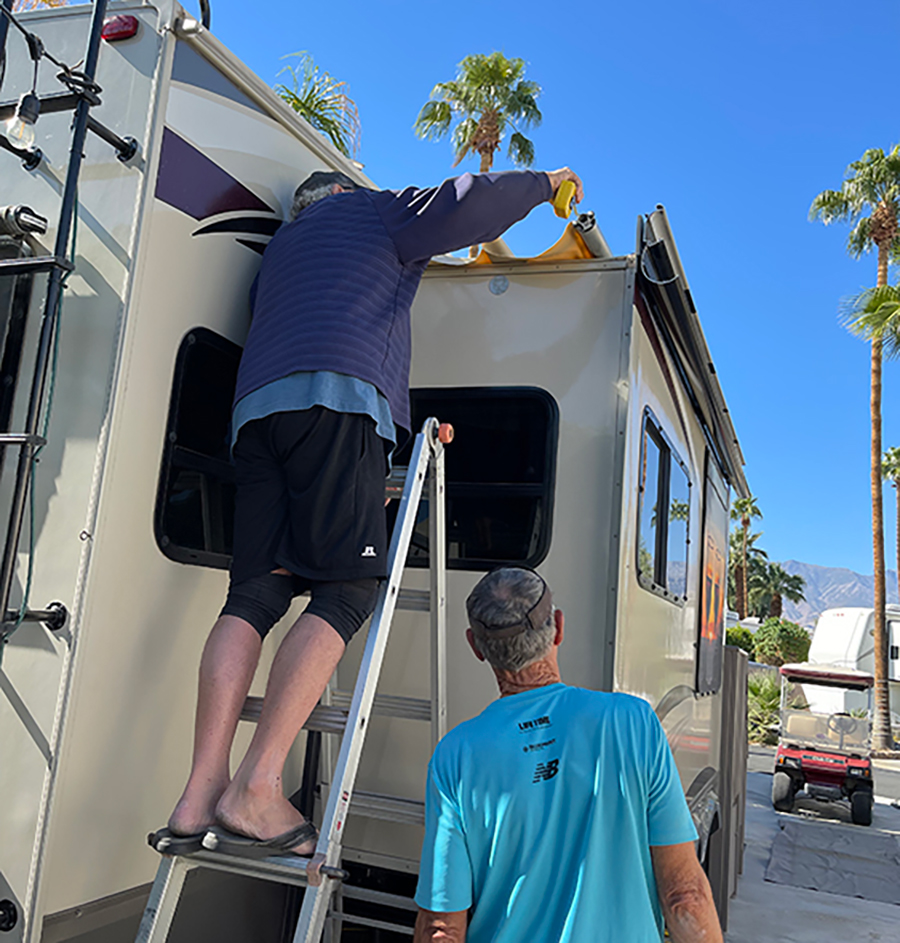
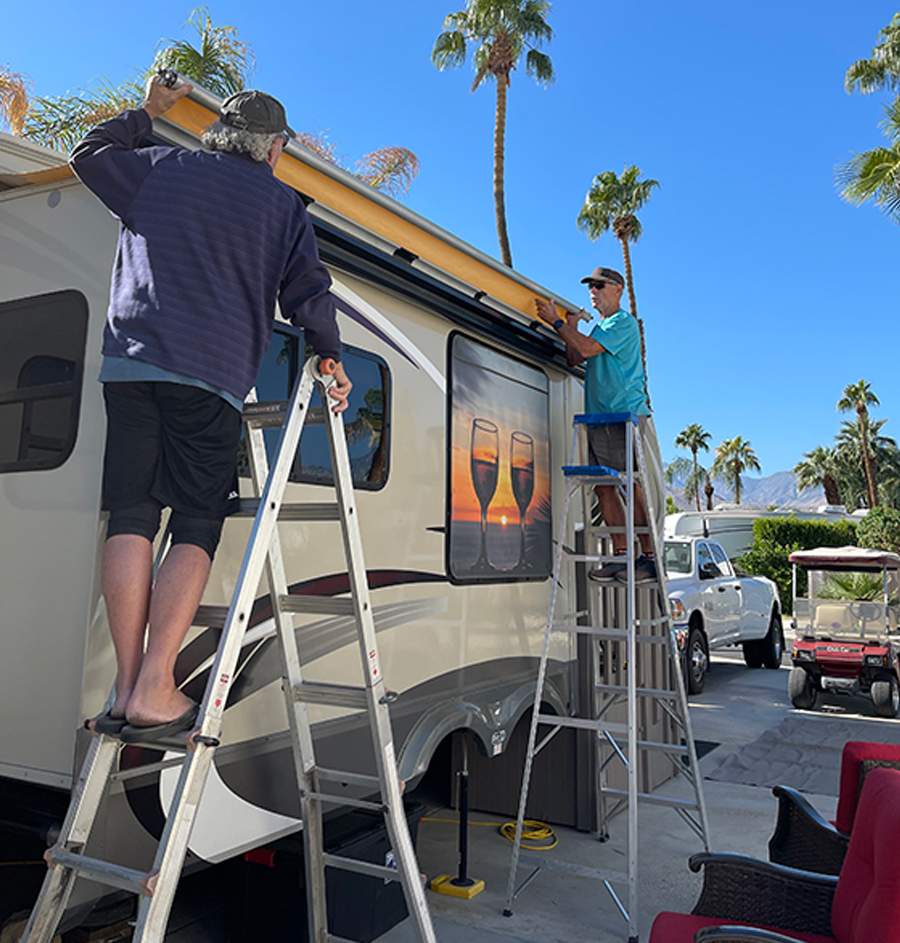
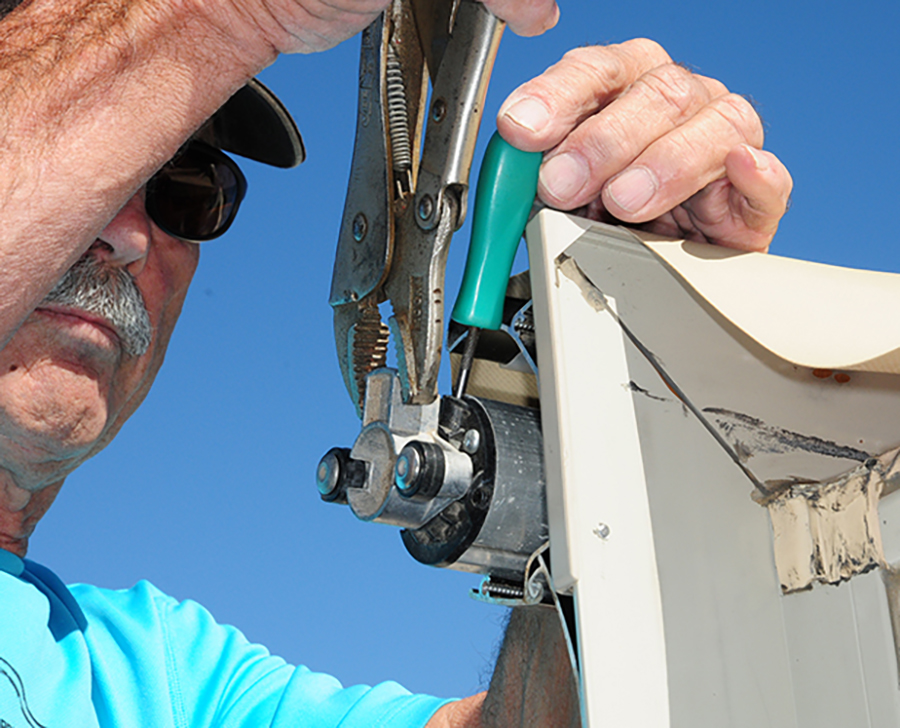
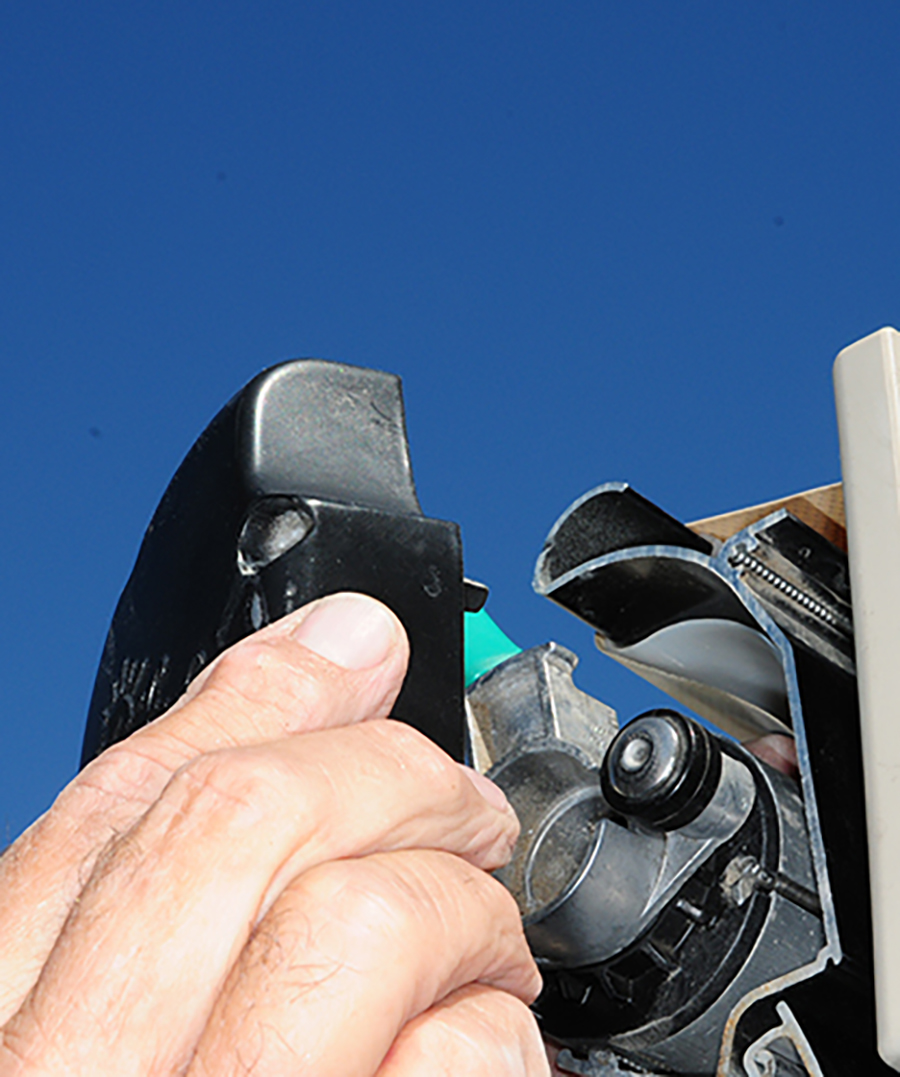
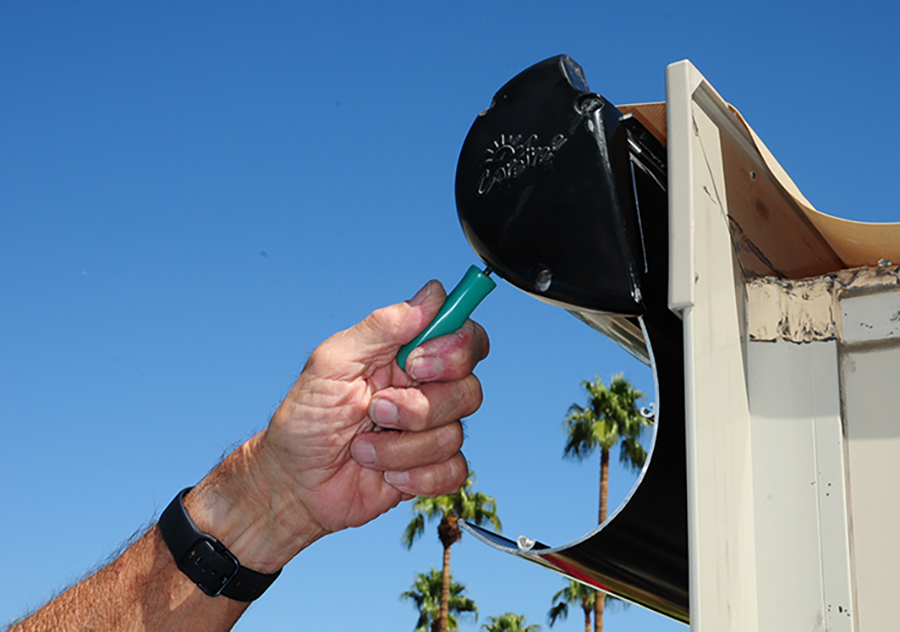
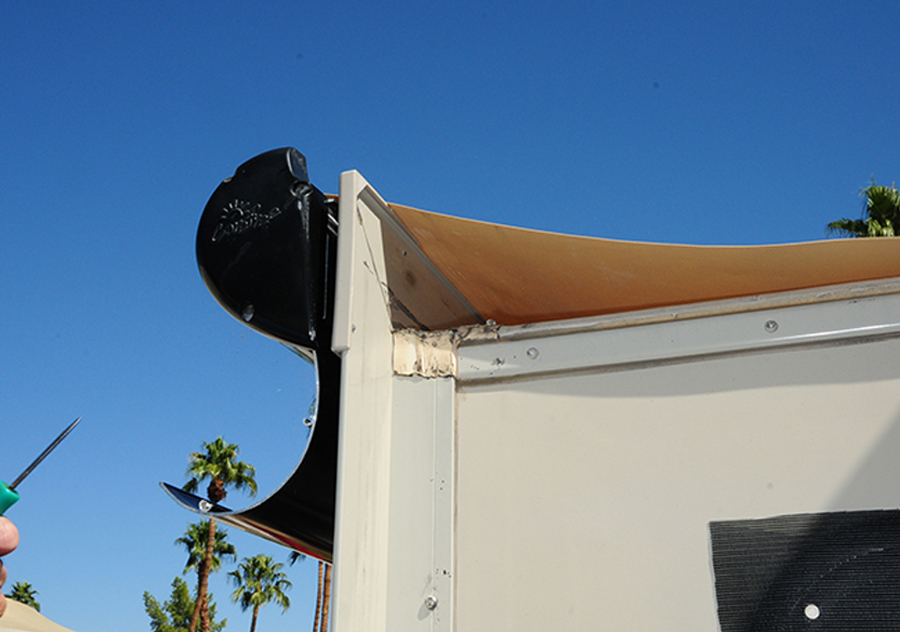
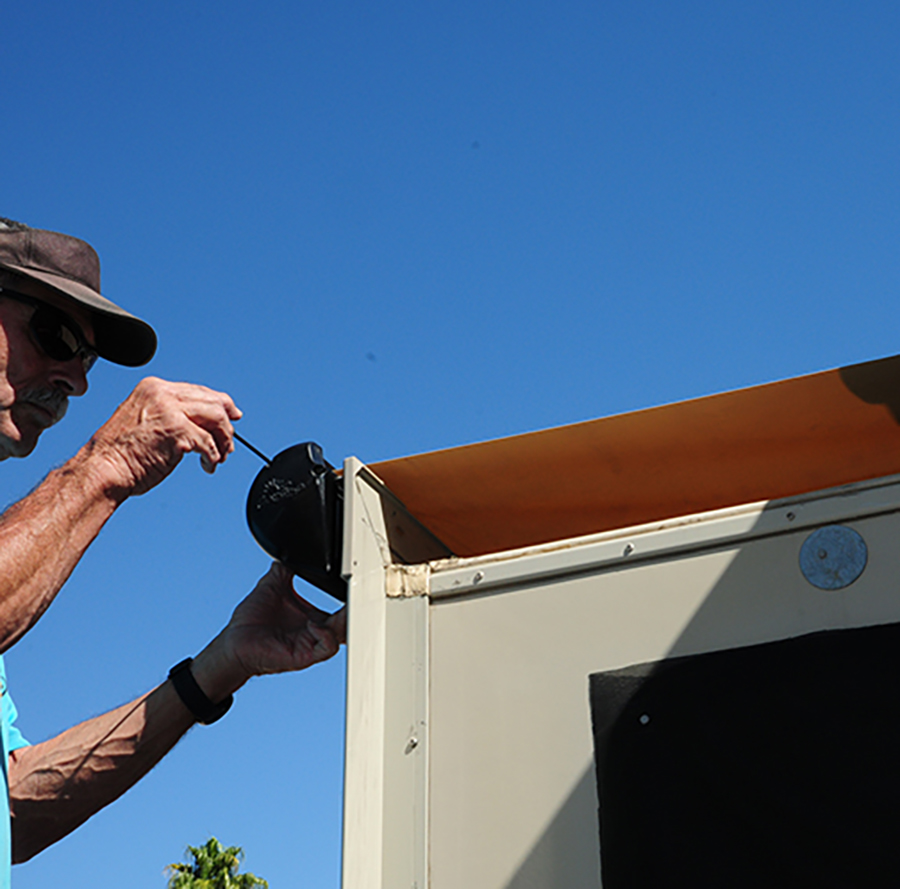